In-line Laser Application on KYMC press
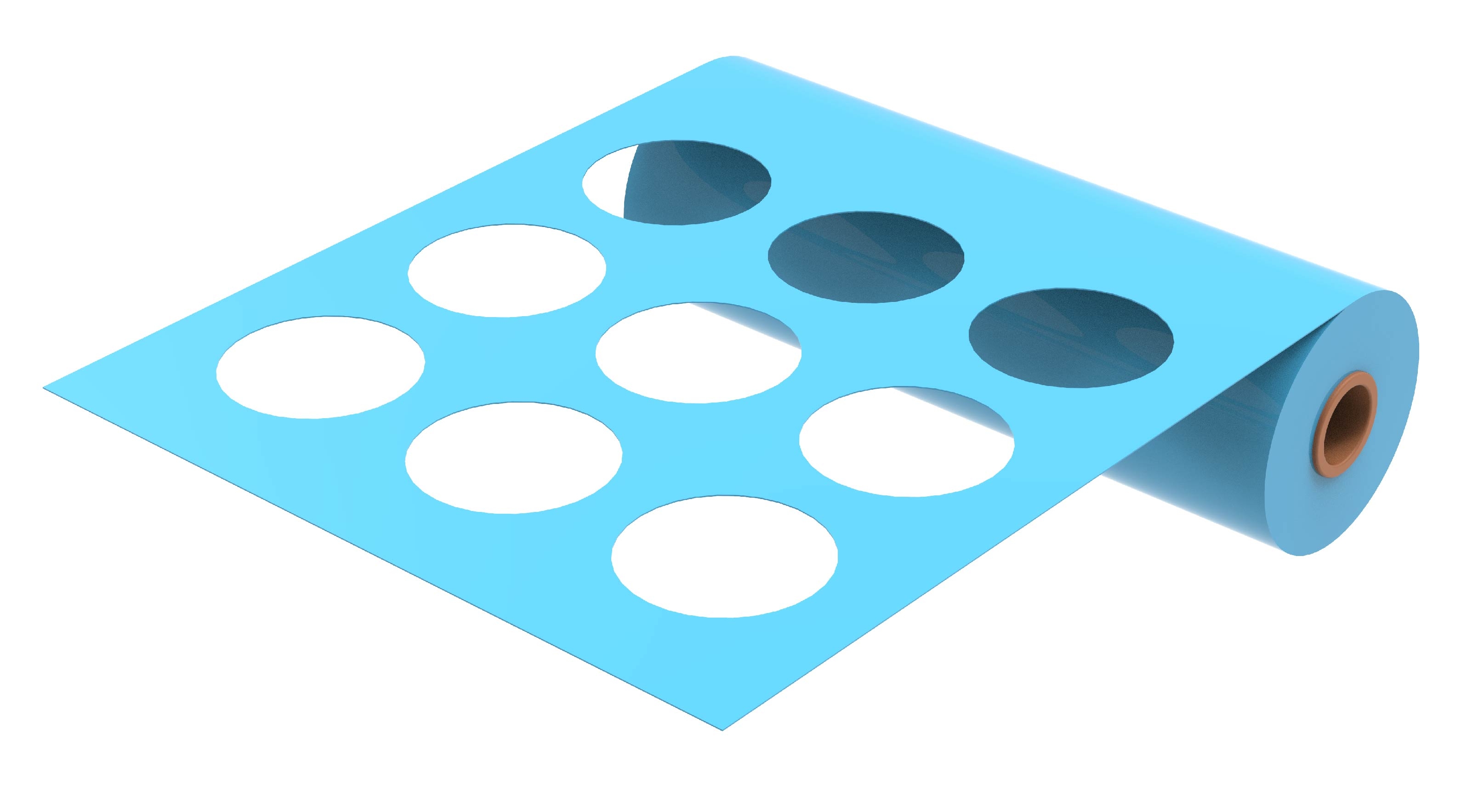
It’s all about the application! Now, there is a better way to produce window packaging, modified atmosphere packaging (MAP) and easy-tear stripes on the packaging. By better, we mean greater flexibility, greater accuracy, faster, less waste, and less maintenance. KYMC is working with laser solution providers to provide our customers with the capability to meet the market application needs in a better way.
Laser technology has been adopted in various industries. In this article, we are going to explore the laser application in flexible packaging on a wide web printing press or on a wide web coating and lamination machine.
Laser Cutting for window packaging
The removal of the window packaging can come in various shapes and forms. Therefore, high production flexibility is required. This can be achieved through cross web laser application (Figure1). The laser can be adjusted efficiently to cut through the materials (Figure 2).
Figure 1
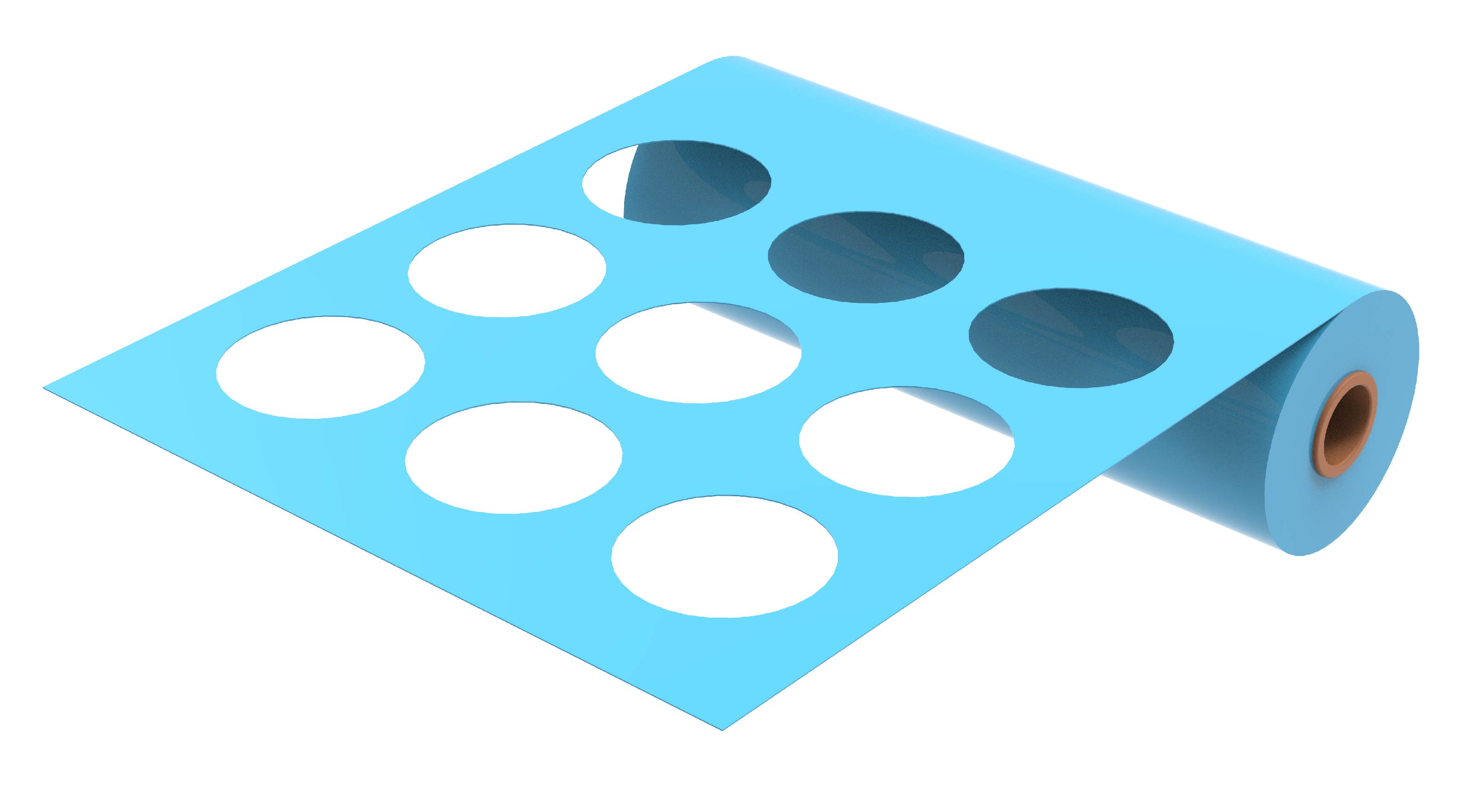
Figure 2
.jpg)
Laser Perforating for modified atmosphere packaging
As the food manufacturers aim to keep food fresher for longer, modified atmosphere packaging or MAP technology is introduced. The idea behind the MAP technology is to create ample of consistent holes throughout the entire packaging to help the regulation of oxygen, carbon dioxide, nitrogen and other gases inside the packaging. This regulated airflow will help to extend the shelf life (Figure 3). The holes that are created need to be adjusted to the right size. If the holes are created too big, it will disable the packaging function when it comes to protection against water, dust and other contaminations. If the holes are created too small, the insufficient airflow rate will impair the ability of the packaging to provide a longer shelf life. Cross web laser can be applied to penetrate the packaging materials at a high consistent frequency without causing a melting effect yet providing a perfectly circular cut (Figure 4).
Figure 3
Figure 4
Laser Scoring for easy-tear stripes
The laser is easily adjustable to provide an accurate amount of energy that is needed to create the score on the packaging. Different packaging materials and different thickness require a different amount of pressure on a cutting knife. Making it difficult to control. Too much pressure will cause the knife the cut through the material. Too less pressure will provide an insufficient score that is needed for easy-tear. With the laser, the cut depth can be control easily with accuracy (figure 5).
Figure 5
The benefits of KYMC laser system over a direct contact die cutter or slitter includes greater flexibility, greater accuracy, faster, less waste and less maintenance.
Flexibility: The KYMC laser system is designed for laser cutting, laser proliferation and laser scoring on various materials such as PE, PET, PP, laminated film and paper. The digital setup and control process allows for rapid work and design change.
Accuracy: The KYMC laser system is designed with operator friendliness for quick and easy setup. The laser is able to deliver precise and selective material removal.
Faster: The KYMC laser system allows for process up to 500m/min on the cross-web laser process.
Less waste: The accuracy and quick setup features allow for minimal waste during production.
Less maintenance: Unlike the direct contact die cutter or slitter, the KYMC laser system does not contact the material directly. The noncontact nature of the process means no downtime due to tool wear or breakage.
KYMC is offering our customers an integrated laser solution. The laser can be installed in-line with the flexographic printing press, in-line with the coating or lamination machine or inline with the slitter and rewinder. KYMC not only delivers the product, but we work with our customers the ensure the solution is fully operational through pre-planning, training, testing, and post monitoring. The intention of the solution is to enable our customers to achieve the ultimate efficiency in its production process. To leverage our customer’s market advantage to get ahead of the game.