Increase Efficiency and Lower Energy Consumption on Your Flexo Press
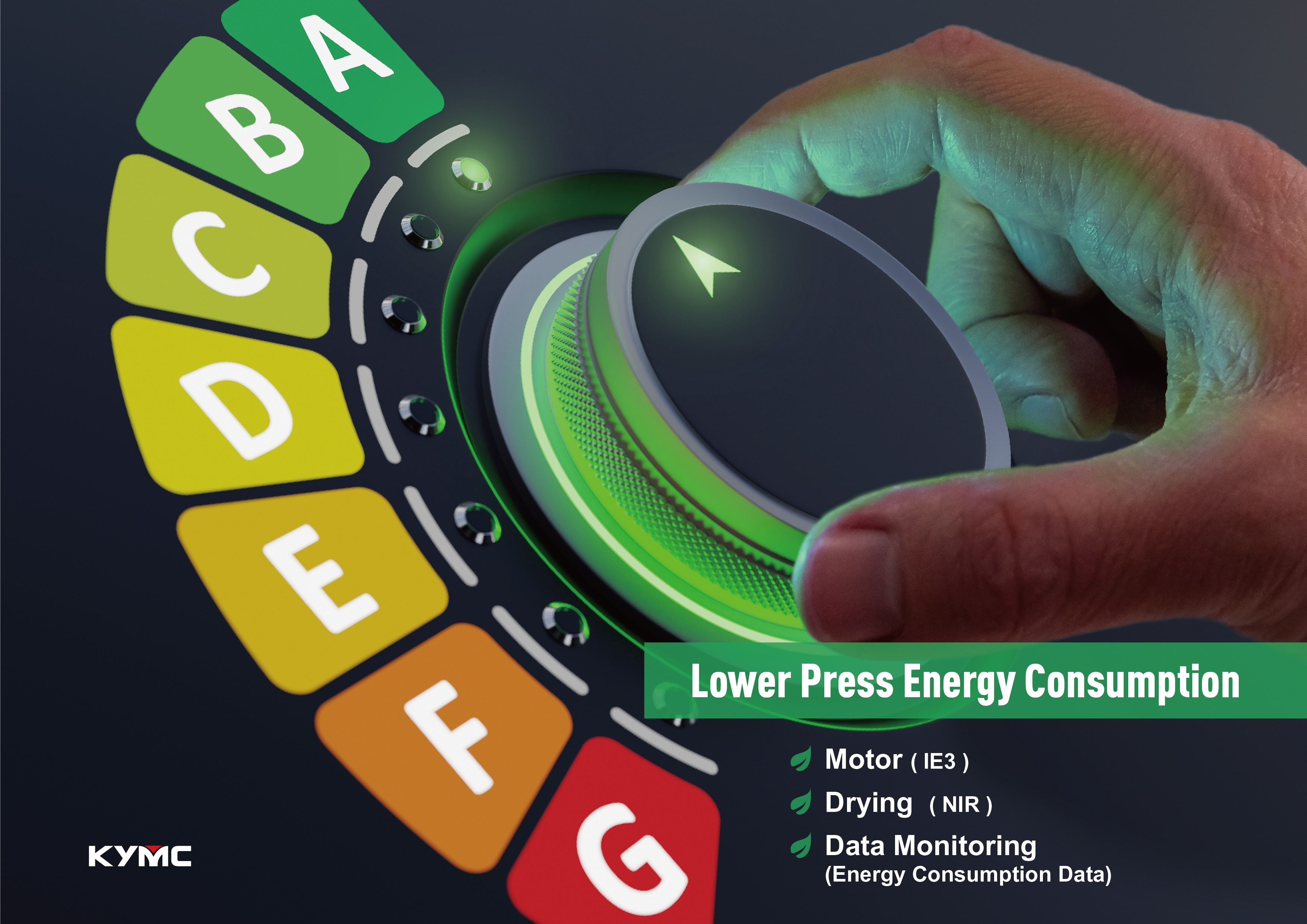
As sustainable development gains importance. Standards and goals are being set at a global level to reduce carbon emissions and ultimately reach net zero emissions. In the latest COP27 (Conference of the Parties), one of the world’s most significant summits on climate change, countries are coming together, reaching a consensus to combat climate change issues. As flexo printers, we can no longer stand on the sidelines. Actions must be taken starting with your own flexo press. There are many ways to increase efficiency and lower energy consumption on your flexo press. In this article, we will explore three different ways including 1. Selection of motor, 2. Drying method 3. Data monitoring.
Selection of motor
In consumer electronics, there are products with a higher level of energy efficiency and products with a lower level of energy efficiency. This is the same for motors. For motors, energy efficiency is the measure of how much input electrical energy gets converted to mechanical energy. A highly efficient motor will consume less energy to yield the desired mechanical energy.
IEC International Efficiency 60034-30-1 standard classifies motors into 4 international efficiency classes. IE1, IE2, IE3, IE4. With IE1 being the least efficient to IE4 as the most energy efficient motor. The impact of motors on energy consumption is great. On average motors account for around 74% of the total energy consumed in production. Therefore, even a small increase in the energy efficiency of the motor will have a big impact on the overall energy consumption.
IE2 motor have an energy efficiency of 92% and IE3 have an energy efficiency of 93.6%. Studies have been conducted to compare the energy consumption between an IE2 motor and an IE3 motor. The more efficient IE3 motor will save around 1580 kWh of energy over the year.
Drying Method
The drying on a KYMC flexo press can be customized according to the customers’ needs. For countries where electricity is more expensive, one can adopt gas instead and vice versa. If water based inks are used, one can adopt a NIR drying method to save energy costs. NIR is an energy efficient drying method that replaces IR + hot air. Not only is NIR energy efficient, but it also removes the issues related to overheating on paper substrates. KYMC has many successful case studies with customers adopting the NIR drying system.
A heat recycling system is also included in the KYMC flexo presses. Feedback was provided by the KYMC clients stating the introduction of the heat recycling system has saved them 23%~35% in energy costs.
Data Monitoring
To have an energy efficient operation, one first needs to understand where he stands. In other words, know where you are so you can set your goals and plan accordingly. KYMC presses provide the data that you need ranging from electricity consumption, gas consumption, ink consumption, solvent consumption, and exhaust emissions. The data is provided in real-time for real-time adjustments. At the same time, data is also provided as historical data for analysis, allowing for mid-term and long-term operation adjustments to optimize energy efficiency.
To make sure that you are in the game for the long run, investments in sustainable development are inevitable. From a global level to the country level and down to the supply chain level are all involved in making whatever we do more environmentally friendly. If you are looking for an energy efficient press or would like to set up an energy efficiency inspection for a potential upgrade on your existing machine. Contact KYMC to improve your press efficiency today.