Automation on a flexographic press
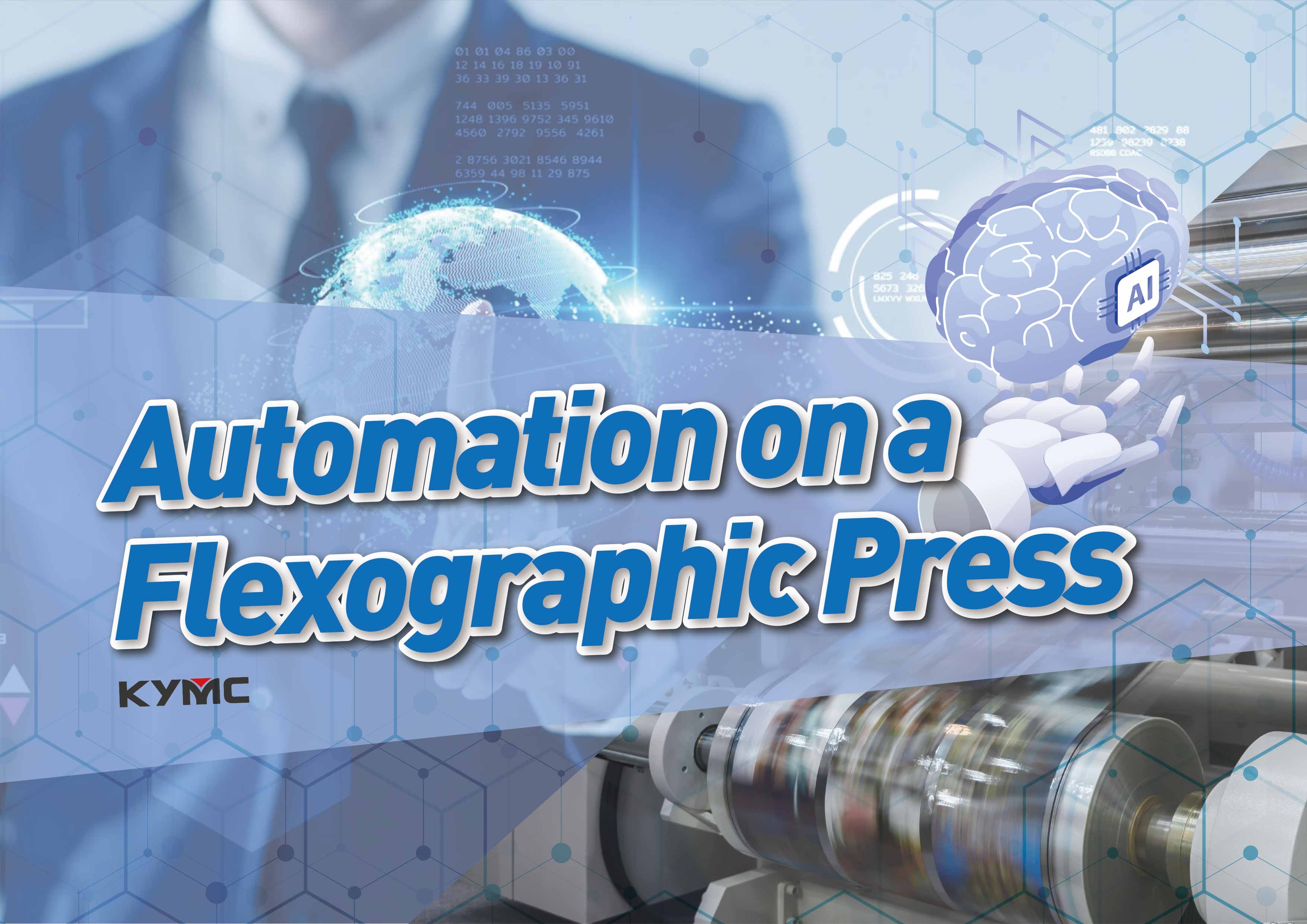
Automation is important. According to Capstone Partners, an investment firm in Boston, USA, the packaging industry players actively adopted technology innovation and automation throughout 2023. Large companies like Amcor and Sealed Air pursued solution models where efficiency was maximized through automation. Many of the Merger and Acquisition(M&A) deals in 2023 were focused on increasing automation at the plant.
To remain competitive in the market, finding a flexographic press that has sufficient automation for the packaging operation is crucial for revenue-generating companies. Flexographic printing is a harder printing process to master when compared to rotogravure printing and digital printing. To succeed in flexographic printing, the experience of an operator is very important. An experienced flexographic press operator knows how to apply just the right amount of impression between the anilox roller, impression roller and the substrate. An experienced flexographic press operator knows where to look for when an undesired print is produced. Is the flaw due to incorrect ink viscosity, incorrect dyne level of the substrate, insufficient drying or the misaligned registration? In short, without an experienced operator, it is hard to achieve an efficient flexographic printing operation. Unfortunately, experienced operators are hard to find. According to FTA(Flexographic Technical Association), The ‘Press Crew’ Crisis: Now Who’s Going to Run My Press?” and “What’s keeping CEO’s up at night? In a survey of 1,409 chief executives around the world, the top business concern among respondents is the availability of skilled labor. For these reasons, many packaging companies shy away from flexographic printing.
The good news is that as technology advances, there are flexographic press automation features developed that will take away many of the dependencies on press operators. Some of the automation features include auto pre-registration, auto impression control, auto ink viscosity control, auto ink temperature control, auto ink washing, non-stop unwinder and rewinder, job memory recall, auto CI drum cleaning, and auto sleeve changeover. Auto pre-registration, auto impression and job memory recall functions can support the operator in getting in-print registration and impression right in the shortest amount of time. The ink-related automation like viscosity control and temperature control will allow a stable ink quality supply to the operation to prevent flaws caused by ink. The auto ink washing, CI drum cleaning, and auto sleeve changeover will allow a quicker job change. The non-stop unwinder and rewinder will allow long-run jobs to run continuously without the need to stop the machine once the substate runs out.
The KYMC flexographic press is equipped with automation features to allow minimum human intervention and maximum operation efficiency. Even better, the flexographic press comes with many ergonomic designs for the sleeve changing, doctor blade changing and substrate setup that will further boost efficiency. Lastly, sensors are positioned at different areas of the flexographic press to return data onto a centralized screen for monitoring, so that the operator can obtain the production-related measures easily and can be automatically alerted if any measures deviate from the norm. If you are looking to increase the efficiency of your flexographic printing operation, reach out to a KYMC representative now to explore the opportunities that lie within our automation features.