Wide Web V.S Narrow Web Flexo Printing
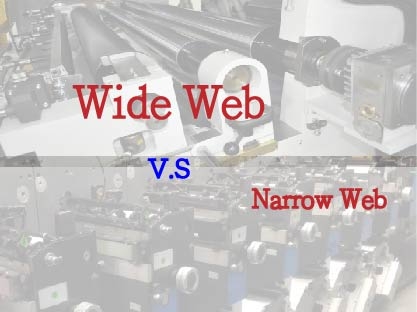
Choosing the Right Flexo Press
In today’s competitive environment, printers need to be as competitive as possible. To be competitive, one needs to choose the right tool for the right job. Wide web flexo press and narrow web flexo press both has its advantages and disadvantages. At the end of the day, it comes down to what your main goal is. For instance, is your main goal to be as environmentally friendly as possible to save cost from pollution emission and to build up a good eco- friendly company image? Is your main goal speed since most of your job orders are very long runs? Is your main goal for printing labels at small quantity?
Press Design
The primary difference between narrow web and wide web is more than just the printing width. Speed is another main difference between the two, wide web flexo press tends to run at speed above 300 meters/min, as for narrow web usually runs between 150 ~200 meters/min. The difference in press speed impacts the formulation of the inks being used. Web wide usually uses faster drying solvent when compared to narrow web. When ink viscosities on a wide web is usually around 25 secs, #2Zhan and narrow web typically are around 35 secs. The narrow web tends to transfer a thicker ink volume onto the substrate.
In terms of press design, wide web is dominated by the central impression design being able to hold the tightest and finest registration, and most narrow web press has a in-line design. This affected the drying designs where central impression often has in-between layer dryers and a final post dryer. As for in-inline design often only have in-between layer dryers and doesn’t have a final post-drying unit. Wide web typically uses chambered doctor blade inking system and narrow web uses fountain rollers inking system. Fountain rollers systems will cause ink to be more exposed to the open air. As result, to be more vulnerable solvent loss and pH variable due to the ink evaporation.
Selecting Press by Application
In general UV ink application are found more on the narrow web, as the cost of UV ink application is greater when compared to solvent and water-based ink application. In terms of press cost, where the higher cost curing systems needed to be added. In terms of the operating cost, where UV curing requires a lot more energy and the cost of the UV ink itself is higher. Therefore, UV application tends to be installed on the narrow web.
The benefit of UV ink is that it dries only under curing, where the photo-initiator within the ink goes through chemical polymerization under UV radiation. Therefore, very fine anilox could be used as the ink doesn’t plug the cells of the anilox, as result producing finer and sharper images. Another benefit of UV ink is that it does not contain solvents, in terms of VOCs emission it is much more friendly.
You Could Consider UV Narrow Web if…
- Narrow printing width
- End product requires higher quality images.
- Order volume is relatively smaller.
- More variable in print design
- Printed product could be sold at a higher price.
- Regulation that places high fees on VOCs emission
You Could Consider Solvent / Water-Based Wide Web if…
- Wide printing width
- End product doesn’t require top quality images
- Large order volume
- Less variability on print design
- Printed product is more price sensitive
- VOCs emission regulation is less mature
There is not an absolute better solution. Select a suitable printing press type based on the end application and the goals that you are trying to achieve.
Article by Daywey Chen, KYMC