KYMC - Glass Conveyance Technology on R2R Equipment
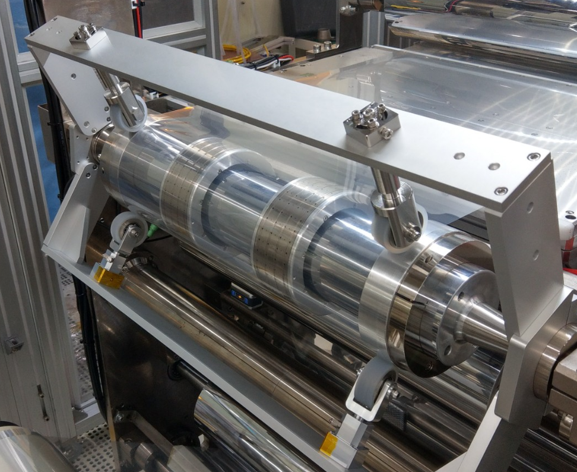
Technology Summary: To print on a 50 μm ultra-thin flexible glass material using Flexographic printing. To achieve a two-layer printing: a conductive grid layer and an insulation layer. The insulation layer will be printed over the conductive grid layer through tight registration.
This is completed on a Roll-to-Roll(R2R) CI Flexographic press, using silver flexographic ink, a low viscosity and a water-based solution containing nanoscale particles for the conductive grids. A dielectric ink, a low viscosity and water-based solution containing epoxy resin for the insulation layer.
An inline near-infrared (NIR) drying module is installed for drying water and sintering the Ag nanoparticles in the silver flexographic ink to achieve high conductivity.
The press is designed so that the printing side of the glass will not contact the rollers, therefore providing a contamination-free production from the rollers.
Two Layer Flexographic Printing (Layer 1: Conductive Grid, Layer 2: Insulation Grid)
Conductive Grid On Flexible Glass
Who will use it?: This innovation is adopted in the Optoelectronics and Display industry. To be applied to flexible products including organic light-emitting diode (OLED) lighting devices and touch panels.
How it will be used?: The printing on the 50 μm ultra-thin flexible glass will serve as a transparent electrical conducting layer.
For small surface area OLED and touch screen electronic devices, an indium tin oxide (ITO) coating is used as a conductive layer. However, for large area devices, ITO alone does not suffice the high and uniform conductivity requirement. In this case, the flexographic printing process can be used to print conductive grids on the pre-coated ITO substrate, to greatly improve the conductivity level and uniformity.
What are the users' benefits?: Conductive grid on transparent glass allows large flexible touch panels to be possible. Traditionally, the transparent(glass) electrical conducting layer is mainly printed using screen printing on a sheet-to-sheet process due to the difficulty in handling glass on a R2R printing process. Glasses are easy to crack and to maintain at a just-right tension.
The sheet-to-sheet screen printing is a much slower process when compared to the R2R process. By replacing the incumbent screen printing with a R2R flexographic process can greatly improve the production speed and lower the production cost. At the same time to replace a multi-step process on screen printing with a one-step process on flexographic printing.