Flexo UV-LED Curing in a Nutshell
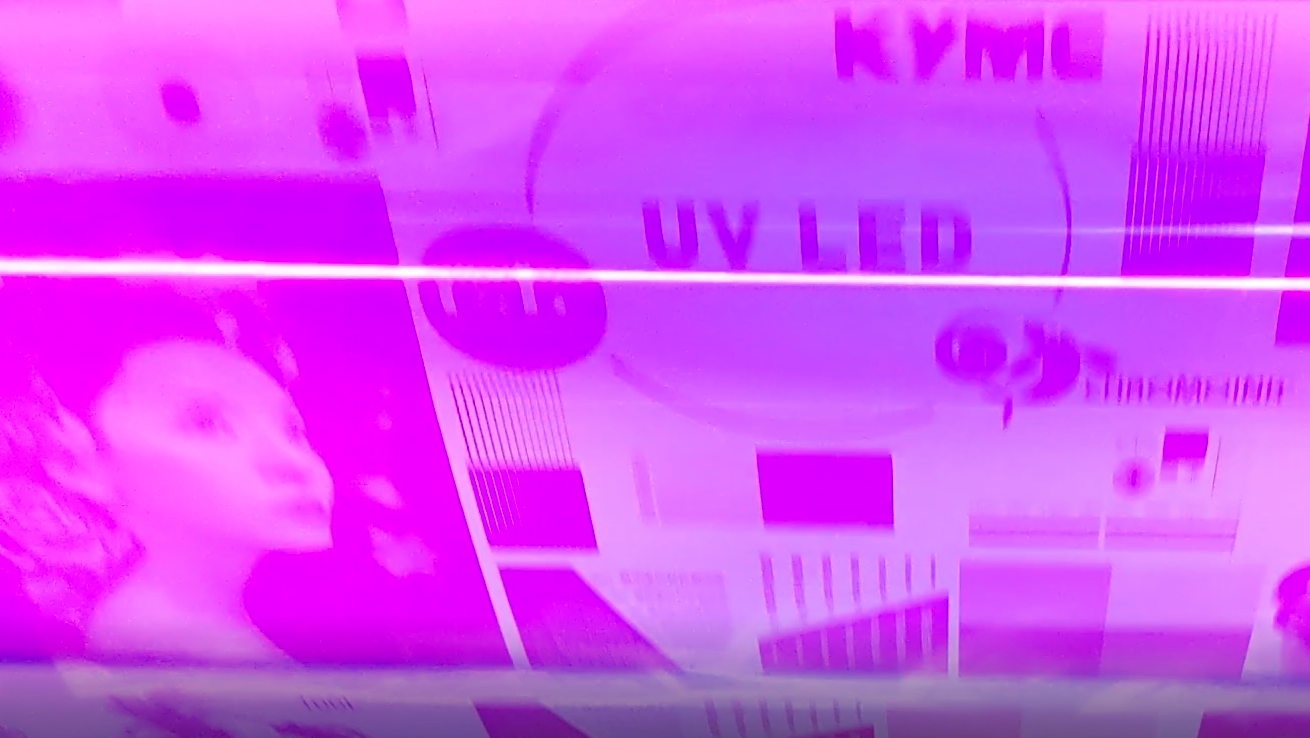
As technology advances printers from the flexible packaging industries are provided with more choices to select from. Inks and their drying methods are among one of the categories where printers have gain access to a variety of selections. The solvent-based ink, water-based ink, UV ink, EB ink…etc. Today we are going to discuss about UV-LED and its curing(drying) method. To explore the benefits and at the same time its disadvantages so that printers can obtain an unbiased review on the UV-LED technology.
Benefits
Leveraged Operation Efficiencies
- The UV-LED curing allows for fasting production speed as it is able to dry the ink faster, especially on bottleneck large surface coverage solid colors.
- The UV-LED curing can be turned on and off in an instant. Unlike the UV lamps, no warmup or cool down time is required, increasing production efficiencies.
- The UV-LED does not transfer heat onto the substrate during curing, therefore there is no waiting time for the downstream converting process after printing. The printed products can go through coating and lamination immediately after printing.
- The UV-LED is known to last for more than 30,000 print hours. As for UV lamps that burn out on average after 1,000 to 1,500 print hours.
Increased Business Opportunities
- The heat from drying has always been an issue to heat-sensitive substrates. The thinner films in general and the PET shrink film. The UV-LED is a solution to the heat issue during drying as it does not emit heat during curing.
- The UV-LED ink is a low migration ink. This opens up business opportunities for food packaging that demands a certain level of food safety.
Higher Print Quality
- As mentioned above, the heat from drying can be an issue as it can lead to substrate shrinkage. The substrate shrinkage will cause registration errors that will impact the print quality. The UV-LED curing will help to take this factor out of the equation.
- When comparing UV-LED to UV bulbs, UV light bulbs burn out from the ends and are constantly degrading. Over time, during production the center of the substrate might be cured, but the edges remain wet. This issue will not exist with UV-LED technology.
More Environmentally Friendly
- The electricity saving of UV-LED when compared with UV curing is reduced by 60~80%.
- UV- LED curing process does not emit VOCs during the curing process. This reduces the hassle to be environmentally compliant.
- UV-LED does not require system fans, blowers and exhaust systems. As resulting providing a quieter surrounding environment.
Disadvantages
Higher Cost
- The initial investment of the Flexo UV-LED equipment is higher than the solvent-based and water-based ink equipment.
- The UV-LED ink cost tends to be more expensive than the solvent-based ink and the water-based ink. There is also a smaller pool of vendor selection for quality UV-LED inks.
Shorter Ink shelf life
- The UV-LED ink is reactive to sunlight. The exposure to sunlight will cause the UV-LED ink to solidify over time. In general, the UV-LED ink has a shorter shelf life than solvent-based inks and water-based ink.
Usually, there is no absolute benefit or absolute disadvantage to a technology, UV-LED is no different. Printers from the flexible packaging industries should weigh the advantages and disadvantages during each investment. If you are looking to become more competitive on the market. Please don’t hesitate to contact a KYMC sales agent to help you evaluate the possibilities out there.
Relevant Reading
Article by Daywey Chen, KYMC