Breaking Down the Drying Process
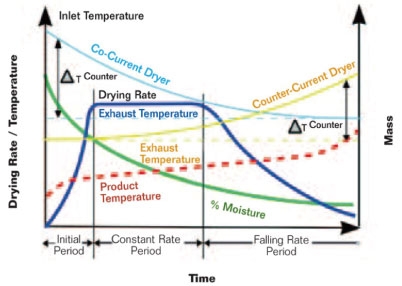
Flexographic printing, coating process, lamination process…etc. Whatever the process may be, drying plays a crucial role in the success and failure of the end result. The drying process is an operation that involves mass transfer and heat transfer. The goal is to maximize throughput at the lowest cost. However, it is not without constraint. To obtain a maximum drying speed, it is not wise to turn up the heat as high as possible as you risk cracking and even burning the substrate. To save as much energy as possible, it is not wise to lower the temperature as much as possible as your product will never dry. Besides considering the constraints related to producing the desired end result. It is also important to consider the constraints related to safety. You do not want to kill people or blow up your plant! The safety constraints mostly relate to solvent usage. It is important to control your solvent level in the drying oven to maintain at less than 25% LEL without continuous LEL level monitoring or at less than 50% LEL with continuous LEL level monitoring. LEL stands for Lower Explosion Limit, meaning the lowest solvent concentration that can lead to an explosion. With all being said, to obtain a high-performing drying system, we first have to understand how the drying process can be broken down into 3 main phases.
Initial Phase:
During the initial phase, this is when the heat begins to transfer to the substrate unless the substrate is already being preheated before entering the drying oven. In this case, the substrate will already be injected with heat. The evaporation rate of the solvents or water will increase sharply during this phase. The moisture will decrease dramatically, meaning the moister will be released into the substrate’s surroundings.
Constant Rate Phase:
In this phase, the evaporation rate will be very high. However, the evaporation rate will cease to increase or alter very little. The moister surrounding the substrate persists on the surface. Therefore, the substrate is protected by the surrounding moisture and a higher inlet temperature will not damage the substrate. Most of the moisture is removed from the substrate in this phase. There is a relatively small increase in substrate temperature during this period.
Falling Rate Phase:
The third and last phase is the falling rate period. During this phase, the drying rate will decrease dramatically, and with most of the moister already removed from the substrate, a high inlet temperature will damage the substrate. Depending on the desired final moister that you would like to achieve, a longer or shorter falling rate period is designed into the system, but in general, the falling rate phase is longer than the constant rate phase.
The three phases are independent, yet dependent at the same time. The behavior of drying substrate behaves differently in different phases. However, the initial drying phase will have an effect on the constant rate phase and the falling rate phase. For instance, if a substrate is dried rapidly in the high moisture range (initial phase), it will continue to dry relatively quickly in the low moisture range (constant rate phase and falling rate phase).
Next, it is also important to understand that there are two types of configurations for airflow in the drying system. One type of airflow system is the co-current drying system (air and material flow in the same directions) and the other is the counter-current drying system (air and material flow in opposing directions). A higher inlet temperature can be used for a co-current drying system because the final substrate temperature will level off in a co-current system. The solids temperature correlates directly with the process air temperature, the co-current design makes controlling the temperature of the dried material much easier. This is ideal for heat-sensitive materials that must be kept below a certain temperature threshold during the drying process. On the other hand, the counter-current system is suitable for substrates with bound moisture that are hard to dry and require heating to a higher temperature.
Understanding how drying is broken down into three different phases instead of one and the two different types of airflow systems will help you in selecting and designing the right drying system with your machine supplier. At the same time, it will help you set up your drying parameters during operation to achieve a balance between throughput and cost control. Contact KYMC to discuss your job requirements and the drying mechanisms that are suitable for them.
Relevant Readings
Co-Current vs Counter Current Drying
Article by Daywey Chen, KYMC
Source: https://www.process-heating.com/articles/86586-the-drying-curve-part-1