Mono Material Market and Challenges
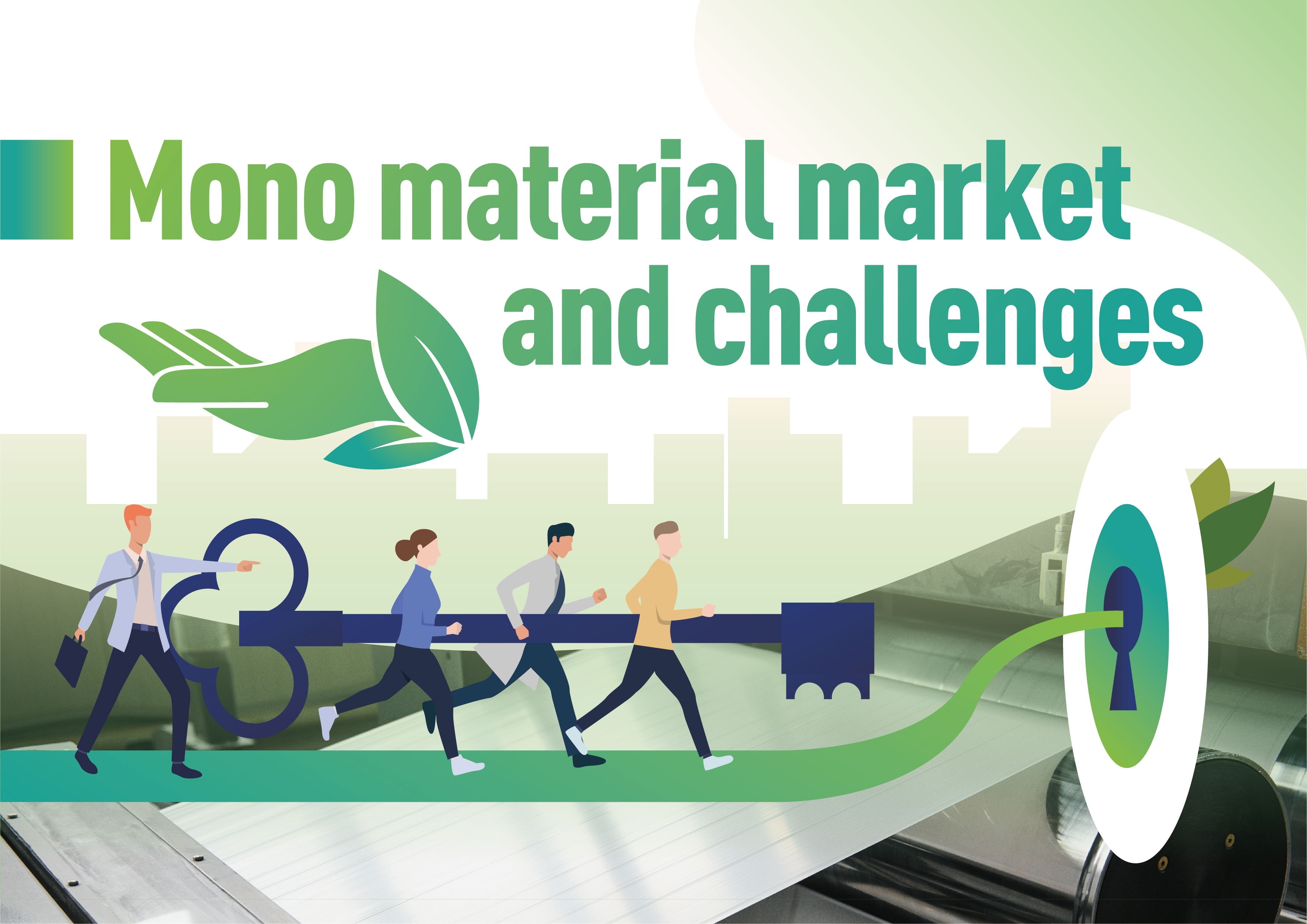
Mono material refers to the type of material that is constructed from a single type of substance or polymer. For instance, materials made entirely of one type of plastic, such as polyethylene or polypropylene. In the context of packaging, mono materials are easier to recycle when compared to multi-substance materials. Mono materials of multi-layers can be separated easily and recycled together. As for multi-substance materials, the different layers are more challenging to separate and often require special processes to separate the different components. Therefore, mono material is considered to be more environmentally friendly. It is the solution to a more efficient recycling system, to reduce negative environmental impact that promotes a circular economy where materials are reused.
Industry and the market are recognizing the importance of sustainability. In an interview with a KYMC customer, they expressed the growth of mono material demand had grown by 250% when compared to last year. Companies are exploring and developing new processes to manufacture mono material substances to improve the recyclability of their products. However, it is not without challenges. There are mainly two challenges to mono materials. Firstly, to maintain the functionality of multi-substance material on a mono material. Secondly, to produce mono material at a justifiable cost and yield rate.
Multi-substance materials are adopted on the market to produce the functionality needed at an efficient level. To make use of the best properties of each substance and combine them to form a single material. For instance, using PE for its excellent sealing properties, and combining it with PET for its excellent temperature resistance, clarity, rigidity, and gas barrier properties. Together, formulate a material that is excellent in performance in multiple areas. When we want to duplicate the functionality of a multi-substance material onto the mono-materials, it will require a special coating and extrusion method. For instance, PE with an EVOH coating or PE co-extruded with EVOH to enhance the barrier property towards gas and oxygen. Wet dispersion coating for applying a metal oxide receptive layer and vacuum coating to provide a barrier layer are also known methods to produce mono material.
When it comes to market adoption, producing mono materials with the needed functions at a justifiable cost and yield rate is very important. From an interview with a KYMC customer, the initial investment for producing a functional mono material is quite expensive. During production, the machine downtime for a typical material is at 2%. However, for mono material production, the machine downtime falls at 20%. On the market, the customers are willing to pay 20 percent to 25 percent more for mono materials over multi-substrate materials. At the end of the day, it’s a balance between cost and environmental impact.
At KYMC we work with many suppliers of mono materials. To work together to ensure that our flexo printing process is compatible with the mono material produced. The KYMC has a strong emphasis on sustainability, where we have a dedicated team to support our customers in becoming a more sustainable business.