what is a flexo printing press?
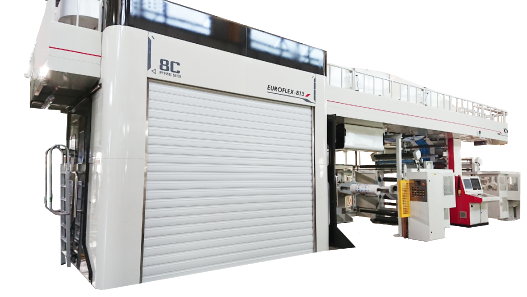
The flexo or flexographic printing press is used commonly in the food packaging industry. The flexo or flexographic press is commonly associated with the plastic industry as many of the food packaging products use plastics. Besides the food packaging industry, the flexo printing press is also associated with industries including paper bags, carton and cardboard box, medical packaging, sanitary product labels, and the diaper industry. In recent years the flexo printing press is also found in the process for printed electronics manufacturing such as RFID, OLED lighting, functional substrates, circuit boards, and sensors.
Lets look into the flexo printing press through a few of its few crucial components that include the anilox, plate, ink, and the substrate.
Anilox
Anilox is the cylinder or the cylinder sleeve on the flexo press that picks up the ink for printing. If we look closely at the anilox under the microscope, we can discover that the anilox is made up of millions of tiny cells for picking up the ink. Different cell shapes pick up ink differently. Some of the common cell shapes include hexagons at different angles, quadrangle, line, and canal. The depth of the cell also comes in many different forms, such as sharp pyramid, flattened pyramid, or a flattened pyramid with a straight cut. The size of the cells also comes in many different specifications measured in LPI or line per inch, the more lines indicates more cells on the anilox. As the cells grow smaller, more cells can be fitted onto the anilox. This allows for finer layers of ink to be picked up, but at the same time, this also indicates that less ink will be picked up as the cell holes are smaller. The volume of ink that is picked up by each cell is measured by BCM or billion cubic microns per square inch. When picking out an anilox suitable for the printing job, there needs to be a balance between the LPI and BCM. The relationship between LPI and BCM is inversely related, meaning the higher the LPI the lower the BCM and vice versa.
Plates
The plate is one of the distinguishing features of the flexo press. Flexo plate is where the printing design goes. Similar to the concept of stamps or letterpress. As the plate rotates on the plate cylinder or plate sleeve, the relief on the flexo plate picks up the ink from the anilox then, transfers it onto the substrate or the printed materials. The flexo plates are made from photopolymers. The production of the plate design goes through an exposure process using CTP technology or computer to plate. The exposure design forms a relief image on the flexo plate. The common way that the relief is structured to form the image is known as plate screening. In general, there are AM(Amplitude Modulated) screening, FM(Frequency Modulated) Screening, and now more commonly XM(cross Modulated) screening.
Ink
The flexo ink for the flexo press in general comes in three different specifications which are water-based, solvent-based, or UV / UV-LED curing ink. The flexo inks need to be fast drying to match the mechanical speed of the flexo press that usually operates between 250m/min to 500m/min. During the printing operation, flexo ink needs to be maintained and controlled at a certain viscosity range, pH range, and temperature range for the optimum print result. Maintaining the ink at a controlled state is a complicated and time-consuming process. That’s why many flexo printing press manufacturers are introducing an auto ink control system to the flexo press.
Substrates
The Flexo press can print on various substrates or materials. This includes porous substrates such as paper, carton and cardboard. For non-porous substrates family including PE, PET, PP, and aluminum. The substrate is fed into the flexo press in a roll form from the unwinder unit. The tension of the substrate needs to be controlled with precision as it moves through the printing and drying units. The capability to main a precise substrate tension makes all the difference in print quality. This is a crucial disguising point for great flexo press and mediocre flexo press.
Having gone through some of the crucial components of a flexo press. Let’s discuss a few common types of flexo presses that are found on the market
The characteristics of the CI flexo press is in its impression system. CI stands for central impression. The CI central drum is a big circular drum in the center of the printing decks. Each printing deck surrounds the CI and each of the printing plate pressure against the CI central drum for its needed print pressure. The substrate lays on top of the CI central drum throughout the printing process. This type of design mechanism enables the CI flexo printing press to hold a tighter registration and maintain a better control on the substrate’s tension. Therefore, allowing for better print quality and high printing speed.
The flexo printing is sometimes integrated with other in-line processes for efficiency. For instance, combined with processes such as extrusion, coating, laminating, die-cutting, embossing, slitting, sheeting, and bag making. This in-line application is found in the production of products that do not require the maximum printing speed and allows for looser print registration control. At the same time the print quality requirement is not that high. Fast Food industry like McDonald's, Burger King, KFC is a group of high-frequency in-line flexo press users.
Stack flexo press is similar to the CI flexo press but has an independent impression roller at each print deck instead of a CI central drum in the center. The stack press is a more economical choice if the printer is not seeking for the best print quality at maximum speed. One of the benefits of the stack flexo press is its capability to perform both surface print and reverse print in one pass, as it has its independent set of impression rollers at each deck.
Lastly, any tool will have its advantage and disadvantage and flexo press is no different
Advantage
- Flexo press, especially CI flexo press has the capability to run at extremely high speed when compared to gravure and offset
- Flexo press has the capability to print on a wide variety of substrates
- Flexo press has a shorter setup time, therefore, reducing waste when compared to gravure
- Flexo press that runs on water based ink or UV / UV-LED inks are much more environmental friendly when compared to gravure
- Flexo press is very suitable for medium to long-run jobs
Disadvantage
- The operators of flexo press requires higher technical skills when compared to the gravure printing process
- Flexo press is less suitable for short-run jobs when compared to digital printing as the job setup time and plate preparation time is much longer and much less flexible.
Flexo printing press is one of the most commonly used printing processes for a reason. Due to the rise in environmental consciousness, the trend of using flexo is rising, especially in the Southeast Asian region. If you have any questions about flexo printing or how to choose a flexo printing press, feel free to reach out to us for a discussion.
Article by Daywey Chen, KYMC