What is flexo printing & How does it work? | Ultimate Guide
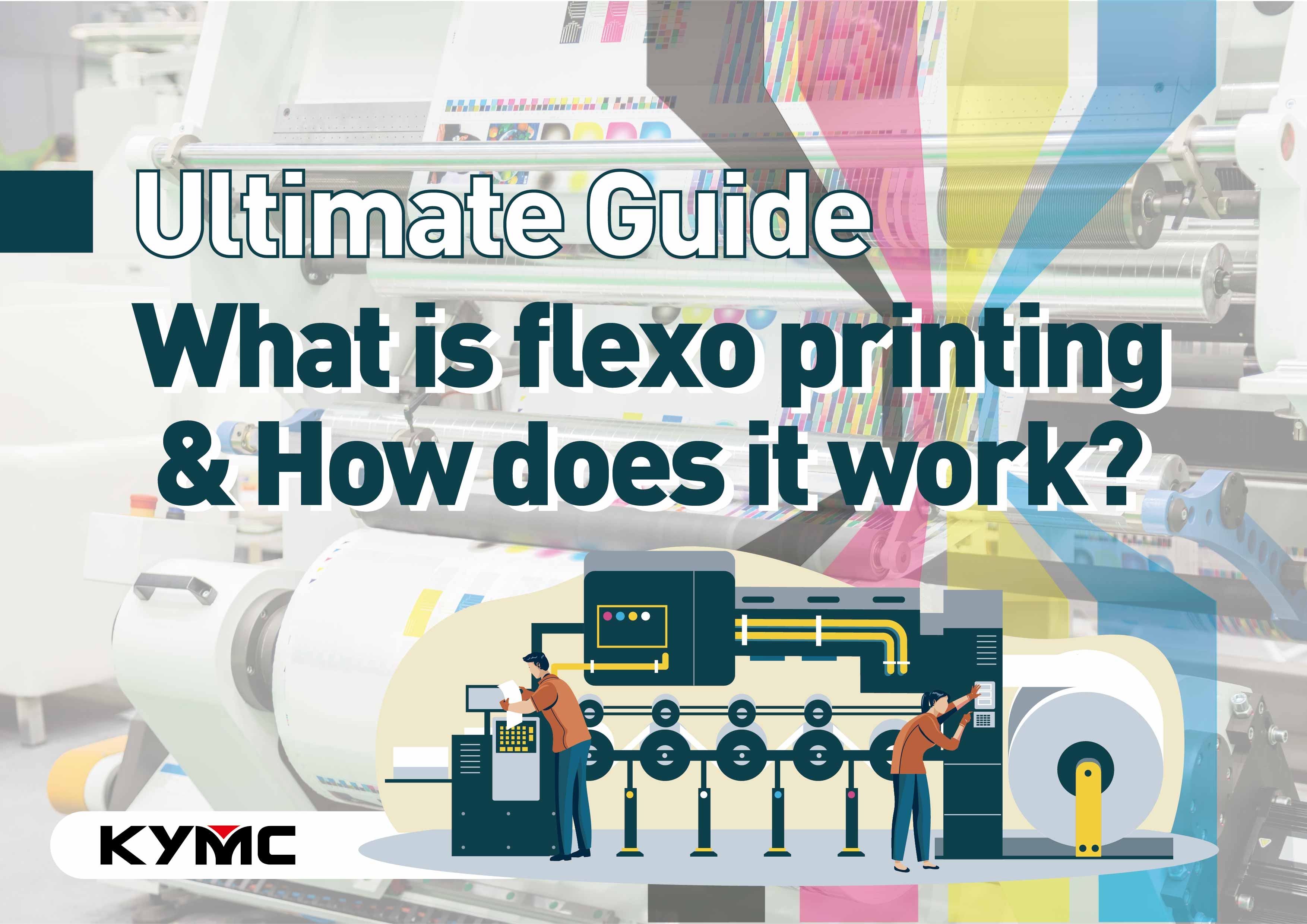
Flexo printing or flexographic printing is a printing process that can be applied to many substrates, including porous materials (paperboards, corrugated boards, paper) and non-porous materials (plastic films). The process can also accommodate various ink types (water-based ink, solvent-based ink, UV ink, and EB-curable ink). It is one of the most common printing methods for flexible packaging, corrugated board printing, paper cup printing, paper bag and plastic bag printing, and sanitary product(diaper/pads) printing.
How Does Flexographic Printing Work?
The roll-to-roll flexographic printing process starts off with the flexo press unwinder, where the substrate unwinds and feeds into the printing stations. At the printing stations, the anilox roller picks up the ink from the doctor blade chamber, then extra ink is wiped off from the anilox through the doctor blades to leave an even and consistent layer of ink. The ink is then applied to the plated image, and with the help of an impression roller, the substrate is pressed against the plate to enable the transfer of the image onto the substrate. Once the image is transferred onto the substrate, the substrate goes through a series of drying before it goes into the flexo press rewinder for storage.’
The key components of a flexographic printing process include a substrate, ink, anilox roller, image plate, doctor chamber, and doctor blades.
The substrate and ink used will greatly affect the drying process. Film substrates are harder to dry as the substrate is less prone to absorbing the ink due to the lower dye level of the film. The paper substrate is easier to dry as it is a porous material that absorbs ink more easily and has a higher dye level when compared to film. A solvent-based ink will be easier to dry when compared to a water-based ink.
Anilox roller comes in different cell shapes including 30, 45, and 60-degree hexagon cells, elongated hexagon cells, and the open GTT…etc. The cells also come in different ink-carrying volumes usually measured in Billions of Cubic Microns (BCMs). Higher BCMs are suitable for a solid printing process, and lower BCMs are suitable for fine-printing images.
The image for the print is designed onto the printing plates. These plates are usually photopolymer plates or rubber plates. The photopolymer plates have resolutions that are usually measured in line per inch (LPI), the higher the LPI, the finer resolution of the image. Therefore, depending on the image you are printing, you may select a lower LPI plate for solid backgrounds, and a higher LPI plate for fine detail images.
Lastly, the doctor chamber and doctor blades are the components that are responsible for applying inks onto the anilox. The doctor blades mainly come in two different materials, metal or plastic. Doctor blades have different thicknesses and different shape designs at the tip such as rounded or lamella. Two doctor blades are installed on the doctor chamber at once. One is called the metering blade and the other is called the containment blade. The metering blade function is to ensure a smooth surface of the ink going out of the chamber to be applied onto the printing plate. The containment blade function is to starch off the remaining ink coming back into the doctor chamber and to keep the ink within the chamber. Together the two blades ensure an even and consistent layer of ink is applied onto the printing plate.
What is Flexographic Printing Suitable for?
Flexographic printing is a great option for long-run jobs (high-volume jobs). The processing speed of flexographic printing can get up to 800 meters per minute which makes it very efficient in producing mass quantify of prints. However, Flexographic printing does require the need for image plate making which makes it undesirable for short-run jobs (low volume jobs). If you are looking for a short-run job, digital printing may be a better alternative. Some companies have combined flexographic printing together with the digital printing function. To have flexographic printing take care of the repetitive designs across jobs (backgrounds) and to have the digital printing take on the various designs across jobs.