SOA for the Printing and Packaging Industry
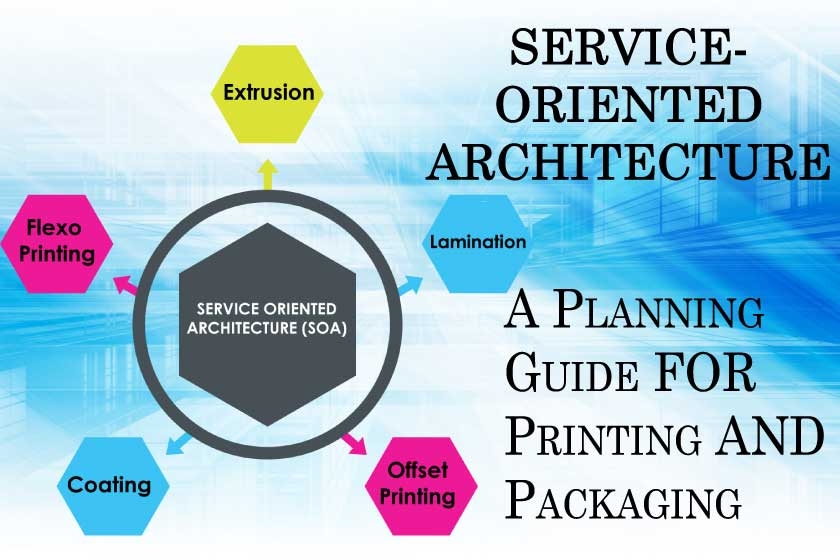
What is SOA? SOA is a term that came from the software industry. It stands for service-oriented architecture. The idea behind this software architecture is that the services, or in other words functions could be broken down into components and be served individually or as a whole, depending on the requirement. Under SOA, the software is no longer designed with multiple functions bundled together that are inseparable. Leading to unused functions burdening up the system and raising up the cost. In a gist, SOA means to take only what you need! And not have to worry about adding or even dropping functions as you go.
The SOA design has worked so well in the software industry because of its customer-centric focus. Users are looking for higher flexibility and efficiency. Why pay more than you need to? If you are not ready to go for the full package, start with the basics and pick up additional functions as needed, and drop out the functions when you no longer need them.
Even though SOA is originally for software development. The SOA principle can be applied to the printing and packaging industry as well when it comes to the production machines. A comprehensive printing and packaging production line from start to finish can include extrusion, printing, coating, laminating, slitting, die-cutting, bag making…etc. It would be great to have the machine capacity from start to finish. However, this may or may not be a realistic approach, depending on your capital and your knowledge to operate the machines. Most printers and converters initiate with a focus on a certain area. For instance, choosing to focus on extrusion only, or choosing to focus on printing only…etc. As time progresses, the printers and converters may receive more requirements from their customers or may decide to expand further into the production line from a business strategy perspective. If that’s the case, then the company will come back to investing in more “functions” or in other words more “machines”.
There are two approaches to the SOA application on machines. One approach is to add additional functionality to the existing machine. The second approach is to add additional functionality in-line. What’s the difference? In the first approach, the additional functional unit is integrated into the existing machine physically. In the second approach, the additional functional unit is physically separated from the existing one but connected indirectly through the web. There are pros and cons to each of the approaches. Attaching different functionalities physically can provide the least waste. The web path for the materials is the shortest and the setup is the most straightforward. This is suitable for businesses that have a fix production steps on a mass production scale. For instance, 90% of the jobs need to go through both coating and printing. Then it makes sense to combine the two functions physically together. On the other hand, when separating the different functionalities physically will increase the amount of waste. However, it provides much greater flexibility. For instance, when only 50% of the jobs require to go through both printing and coating at the same time. Others require either printing or coating only. In this case, the separation of the functionality will be the most suitable to achieve the highest flexibility where different functionality can run in sync or separately.
In order for the SOA application to work, the different functionalities need to communicate with each other. Communication between the different functionalities includes control and monitoring. Control refers to feeding data to the different functional units simultaneously. Is there a central platform for the operator to send out directions or does the operator need to go to individual functional units to deliver the job instructions? When the operator sets the machine to run at 300 meters per minute, will the different functionalities run in synchronization? When the operator needed the machine to stop, will the different functionality stop in synchronization? Monitoring refers to data coming back from the functional units. Will the operator be able to get access to data from one central platform, or does the operator need to read off the information from different HMI scattered in different places?
KYMC has ample experience in providing the SOA application to our customers. Being able to deliver a direct physical connection or indirect physical connection is only one part of the story. At the end of the day, how well do the different functionalities communicate with each other is what makes a success. The SOA application has one goal in mind, to increase customer flexibility, efficiency and to drop cost.
Article by Daywey Chen, KYMC