Find out if you are ready for ECG printing
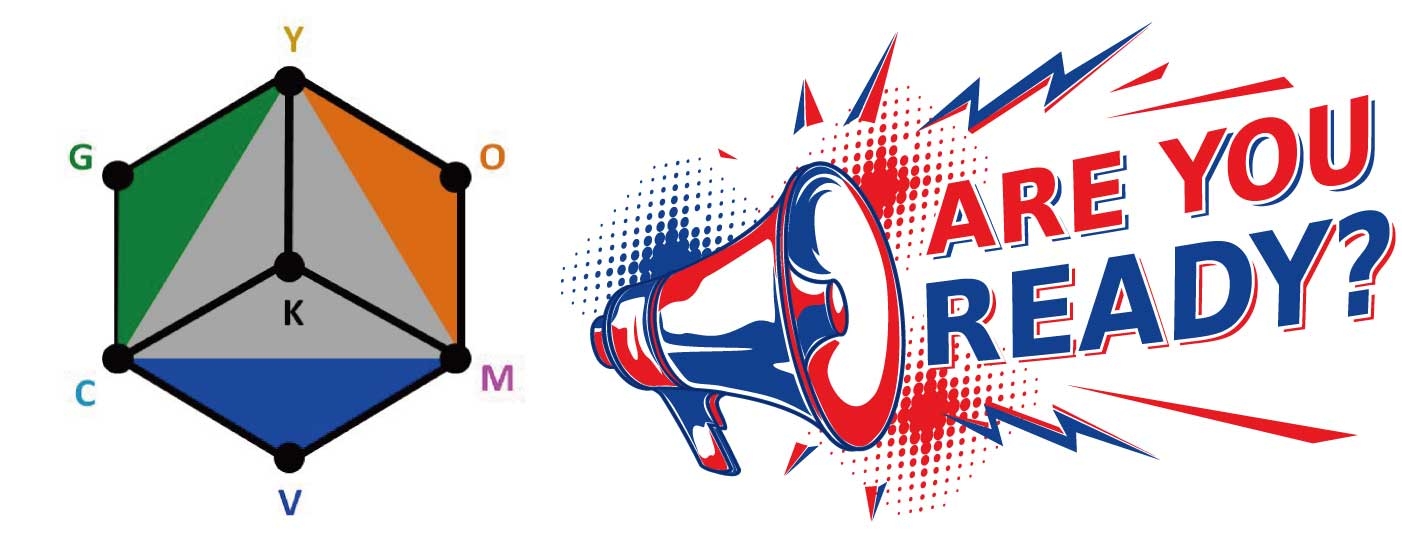
Let’s start off by exploring all the good stuff about ECG printing (Extended Color Gamut) and why it has become such a trending target in recent years. Notice that I used the word “target”. This implies that there is usually a gap between the ECG concept and the production floor reality.
What is ECG?
ECG refers to printing beyond the CMYK four-color process by adding three additional colors, typically orange, green, and violet. By adding three additional colors will help to achieve a larger color gamut than the traditional CMYK four-color process. The goal of the ECG is to replace the need for spot colors (specialized color) with the 7 sets of fixed colors.
Why ECG?
The idea of adopting the ECG process is to prevent the need for spot color change. Therefore, saving time and operational cost in color changing. When it comes to color changing, it involves washing and changing of the anilox, chamber system, pipes, and tanks. In short, the color change is a time-consuming process that printers would like to minimize. ECG is receiving greater attention in recent years because as print jobs are getting shorter and shorter. The number of job-change requirements is increasing. If the printer is able to set 7 colors to cover all jobs, then it prevents the need for color change during job-change. This will greatly reduce the job-changing time. Money is generated during press operation, not during job setup.
The benefit of ECG sounds great. However, it is more easily said than done. At the end of the day, if your operation is not ECG-ready, then we strongly advise you not to attempt it, it may cause more harm than benefit to your production. Now, let's examine if you are an ECG-ready company?
Are you an ECG-ready company?
Print jobs
What print jobs are you taking on? What’s the Delta E value that your customer is willing to accept. Let’s be real. ECG is not going to be an all-inclusive process to cover all types of print jobs. ECG is suitable for print jobs that are fully covered with print and do not involve gradient designs or the fading of colors. The print jobs that do not involve highlighted areas. Print jobs that are similar in design and require minimal adjustment. For example, the Lay’s potato chips product series match the criteria above (Figure 1). An example of a print job that is less suitable for ECG will be a diaper print job (Figure2). As you can see diaper print jobs often include a photo of a baby, which requires highlights in the facial area, and gradient color designs to make the skin look smooth. The gradient design is then extended to many parts of the print to generate a softness feel. At the same time, there will be areas that are unprinted. Therefore, if you are taking on jobs that are similar to the diaper sample in Figure 2. Think twice before adopting ECG.
When it comes to the Delta E value. From our market experience, if your customer is unable to accept anything greater than a Delta E value of 2, you can also think twice about it.
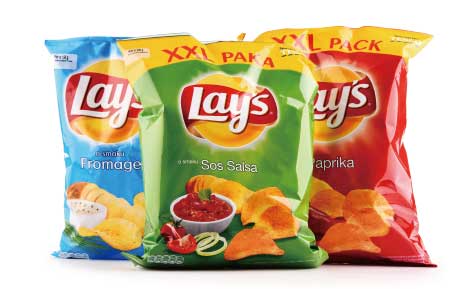
Figure 2.
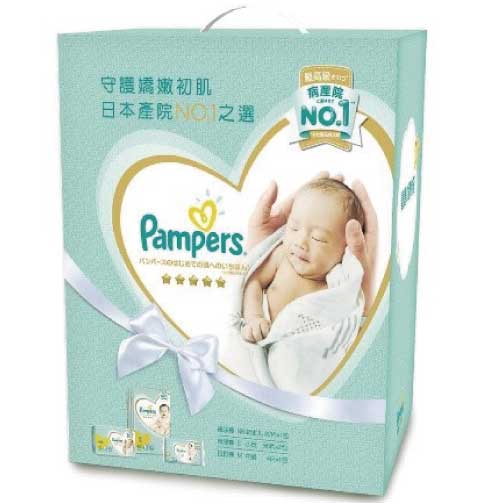
Ink
Ink is one of the most crucial factors when it comes to becoming an ECG-ready company. Printers need to work very closely with their ink supplier. Supplier in the singular! This may be a detrimental area in ECG printing as the printers are more likely to be bonded to one ink supplier. On the other hand, good news for the ink supplier! The reason that the ink supplier becomes less replaceable is that in ECG printing, each batch of ink needs to be very consistent. The L*a*b value of each batch of ink needs to be close to identical. The set of ECG ink for each printer may be different depending on the type of jobs and the type of equipment that the printer has on hand. In practice, it takes much time to work out the needed seven colors with the ink supplier to come up with the best match. Therefore, making the ink supplier less replaceable.
Press
Let’s have a closer look at the printing press. During CMYK + spot color printing, printers have the spot colors to reproduce a portion of the colors directly. To use spot colors to obtain what you see is what you get. However, with ECG printing, this luxury is taken away. All the Pantone colors for the print needs to be produced through the 7 colors halftone process. The interdependencies of the colors are much higher. In CMYK + spot color printing, you have high color dependencies in the four colors CMYK, and less color dependencies in the spot colors. When your spot colors are off, it will have less effect on the other print areas. However, with ECG, you now have 7 colors that are highly dependent of each other. What does this imply? This implies the printing press needs to be extremely accurate in its registration control. This includes stable tension control, a sensitive edge guide system, and excellent bounce control. Each color in the halftone process needs to be printed with extreme accuracy with minimal dot gain. The press makes all the difference!
Operation
So far, we have talked about the print jobs, the ink, and the press requirement for ECG-ready. However, that’s not all. Operation is crucial to the success of ECG-ready. Operation includes many things. Are your anilox carefully looked after and cleaned to ensure that you have a consistent and precise delivery of the ink at each job? Are your substrates in good shape and has the needed dyne level for the print job? Are your operators carefully monitoring the conditions of the work environment to maintain a constant temperature and humidity? Are your operators following the standard operating procedure each time to set up the print job? In a gist, the more identical replication that you are able to make out of your operation, the better chance for you to succeed at ECG printing.
If you take away nothing from this article, just remember this. Flexography printing is a comprehensive set of processes and equipment working together in synchronization under controlled conditions. When it comes to ECG printing, double that requirement! KYMC knows that to most printers, it is too much to ask for, that’s why we have done most of the hard work for our customers. Please note that I mentioned Most, not All! If you are unable to have your operator properly clean up the anilox to maintain the same BCM cell volume, then there is nothing KYMC is able to do about it. However, KYMC has done what’s possible on our side to take you closer to becoming ECG-ready. KYMC works with many of the supply chain vendors to get you jump-started. This includes working with Esko on the plate making and color management software. To work closely with Apex on the anilox for the most suitable line screen, cell volume, and cell shape combination. To work with Rossini and Rotec on the printing sleeves. To work with Toyo Ink, DIC and Siegwerk on an initial set of ink formulas that is suitable for the ECG process. Most important of all, to deliver a press that is capable of reaching extremely tight registration under high operational speed to close the loop. Providing a total solution has always been one of KYMC’s core values. KYMC is confident to help our customers in becoming an ECG-ready company. KYMC is ready. Are you?
Article by Daywey Chen, KYMC