Flexographic Press - Gearless Servo V.S Geared
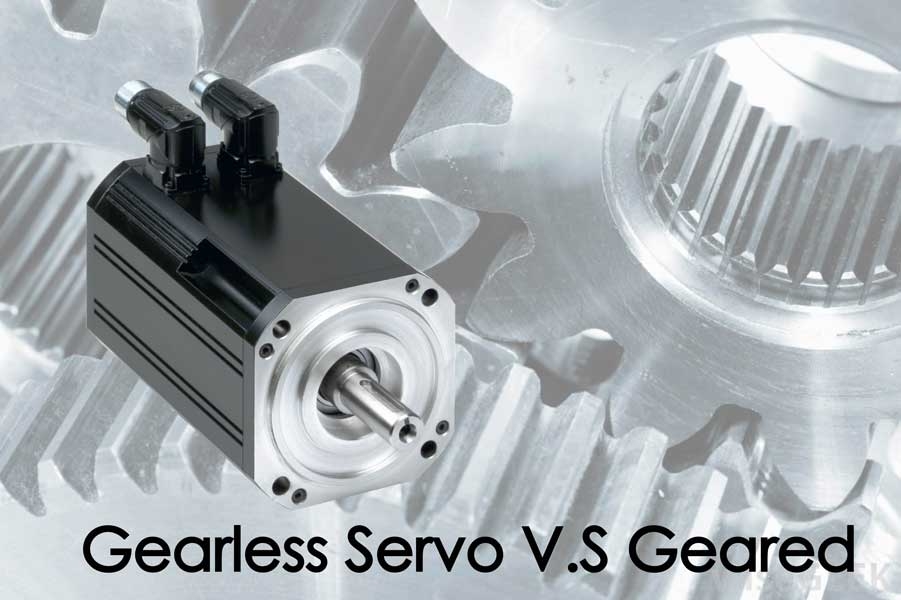
Why is Servo Gearless More Precise?
To understand why a servo gearless is more precise, we need to understand what is affecting the print precision in the first place. The accurate synchronization of the anilox roller and the plate cylinder at each print deck plays an important role in print precision. In the flexographic printing process, the anilox roller contacts the plate cylinder that carries the plate with dot patterns that form the print image. During the contact, ink is transferred over from the anilox roller over to the dot patterns. To be able to provide a constant ink coverage is crucial to the print quality and this depends on maintaining consistent motion between the surface of the anilox roller and the plate cylinder. Whenever the print cylinder moves faster than the anilox roller, less ink is transferred to the print cylinder, resulting in a light section
in the printed piece. Whenever the anilox roller moves faster than the print cylinder, more than the normal amount of ink is transferred, resulting in a dark section.
Now, knowing what affects the print precision, let’s look into the mechanism of a geared press and a servo gearless press.
Mechanism - geared press
To synchronize the anilox roller and plate cylinder in a geared press. The anilox roller and plate cylinder are geared together, driven by a single motor as shown in Figure 1. This type of mechanism creates a backlash in the geared system. Backlash causes the roller and cylinder to rapidly accelerate and decelerate as the gear teeth bounce back and forth against each other. This is inevitable even when a geared system is tuned very tightly, within time the gears will wear, and backlash will begin to occur again as shown in Figure 2.
Figure 1. Geared system powered by a single motor to drive the movement at the impression cylinder, plate cylinder and anilox roller.
Figure 2. Backlashes are the extra spaces between the gears causing misalignment in the rotations.
Mechanism – servo gearless press
The direct-drive rotary servo motors synchronize the anilox roller and the plate cylinder to a much higher level with precision without the mechanical gears. The servo gearless mechanism eliminates gearing together of the anilox, plate and impression cylinder through a single motor. Instead, each anilox plate and impression cylinder has an independent servo motor driving it as shown in Figure 3. The motion of the anilox and plate cylinders are electronically synchronized by a closed-loop control system. The motion feedback device provides the servo motors with far more accurate position and velocity information that the controller compares to its programmed motion profile and based on this signal sends velocity commands signals to the amplifier that drives the servo motor. As result synchronizing the anilox roller and plate cylinder in both speed and phase with precision.
Figure 3. Individual servo motors, each driving the impression cylinder, plate cylinder and anilox roll independently
When is a Servo Gearless More Precise?
Registration needs to be held throughout the printing process. This includes maintaining registration during constant printing speed, during acceleration/deceleration and after acceleration/deceleration. The servo gearless press not only maintains better registration during a constant printing speed but more importantly during and after acceleration/deceleration. In a geared press, due to the backlash from the gearing mechanism, leading to a lower registration tolerance during and after acceleration/deceleration. Therefore, much time and effort are required for registration adjustment after each press acceleration/deceleration.
Other Advantages of Servo Gearless Press Over Geared Press
- Auto pre-registration is possible on a servo gearless press since the anilox roller and plate cylinder are driven by individual servo motors which are able to provide roller and cylinder position information back to the controlling system for configuration. To provide a tighter registration from the start before printing begins. As result, reducing setup time.
- Job memory for repeat tasks is possible as historical servo motor data can be stored in the system. This will reduce the setup time.
- The tighter registration control allows for a higher printing speed, improving the overall production throughput
- The tighter registration improves the yield rate of the production, generating less waste.
- More precise registration adjustments, as the servo motors, allows fine-tuning to 1 micron.
- Mechanical simplification as the part count on a typical bill of materials is reduced. On a geared press we have parts such as motor, gears, lubrication system, oil bath, filter, pump, sealed housing, shafts, and bearings. As for a direct drive gearless press, we have servo motors. This translates to faster assembly, less maintenance, and less overhead to purchase.
- The servo motors generate a lower noise level when compared to the gears bouncing off each other. This will be beneficial in industrial environments where the maximum allowed audible noise level is regulated.
When evaluating a flexographic printing press to invest in. There is no absolute right or wrong. If your production does not require a tight registration, labor cost is comparatively cheap, material cost is low and production volume is low then a geared press may be suitable. If your production requires tight registration, labor cost is high, material costs is high and production volume is high then a gearless servo press may be suitable. When accounting for the press cost, we should not only look into the initial cost but to include the production and maintenance cost as well.
Source:
https://www.kollmorgen.com/uploadedFiles/kollmorgencom/Service_and_Support/Knowledge_Center/Articles/DirectDrive_Printing_08-09_FLEXO.pdf
Article by Daywey Chen, KYMC