Do you have control over your ink viscosity?
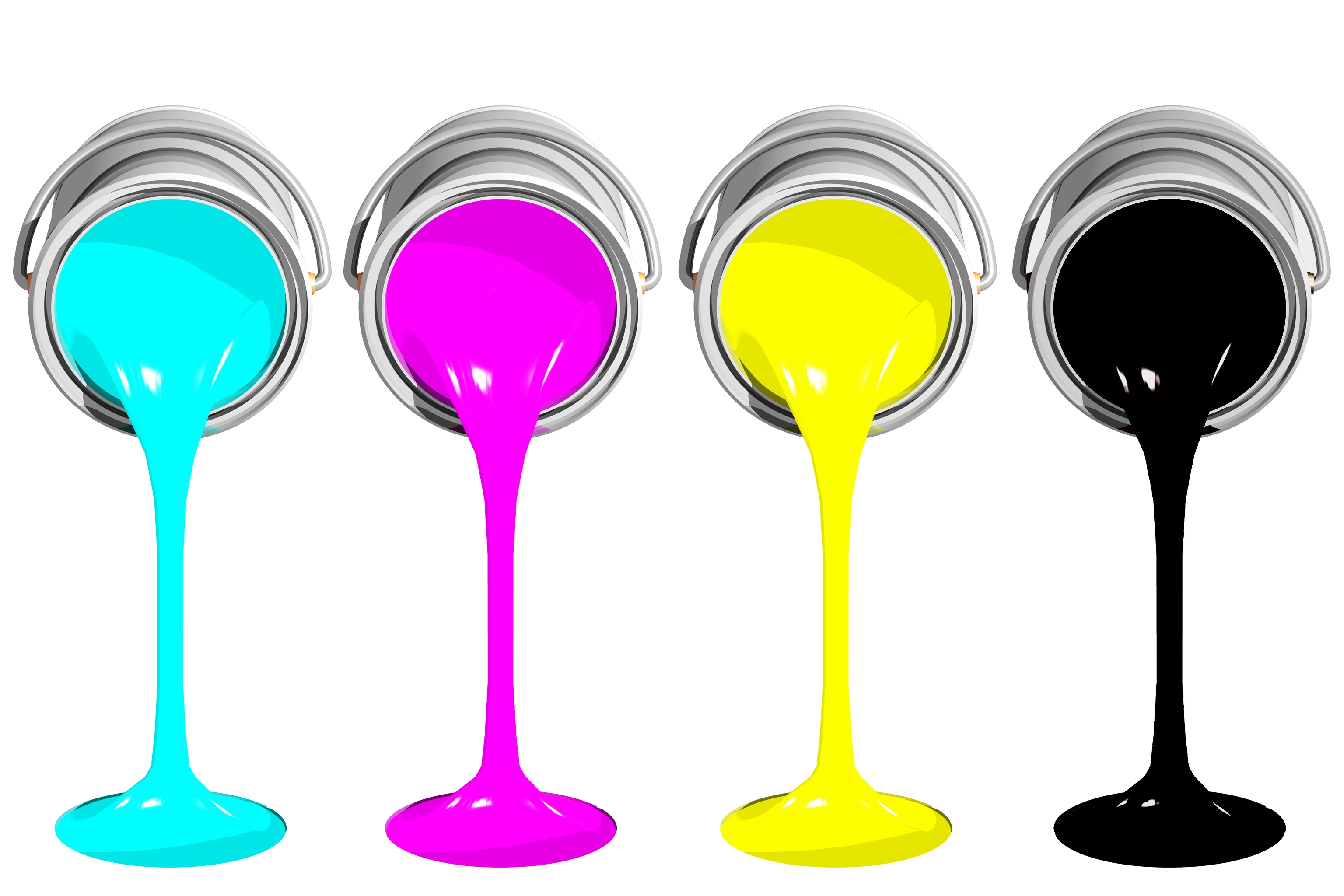
How important is it to have control over your ink viscosity? Ink viscosity affects how well your ink is able to transfer over from the anilox to the plate, and from the plate onto the printing substrate. It affects how well your ink will dry on the substrate. In general, your press production speed, and the quality of your print is highly correlated to the ink viscosity. In Flexographic, having a suitable ink viscosity makes all the difference.
However, how confident are you with your ink viscosity? Your confidence level should relate to how you quantify your measurement. To quantifying your ink measurement, there are a few common methods that are used including 1. Zhan cup 2. Falling Sphere Viscometer 3. Vibrational Viscometer.
Zhan cup is a cup-type viscosimeter that measures the viscosity of the ink by flowing a definite volume of ink through the cup. The time (seconds) required for the ink to flow through the cup defines the viscosity of the ink. The advantage of using a Zhan cup is that it is simple to use and requires no special skills. Zhan cup is convenient as it is small and lightweight, at the same time measurements could be done quickly. However, the disadvantage of the Zhan cup is its accuracy, even for an experienced operator. Zhan cup is used together with a stopwatch. The timing of starting and stopping the stopwatch can vary from operator to operator and from trial to trial. The measurement can easily differ by 2~3 seconds. Furthermore, during the printing operation, due to factors like temperature and humidity, the viscosity of the ink is likely to alter. This means that the operator will need to constantly re-measure the viscosity of the ink throughout the operation. At the same time, constantly readjusting the ink to achieve a constant viscosity.
Falling Sphere Viscometer drops a sphere with known density and dimension into the fluid sample and measures the time it takes for the sphere to fall to a specific point. Falling Sphere, like the Zhan cup are both flow-based system. Often the Falling Sphere methodologies is equipped with sensors to capture data digitally. When compared to the Zhan cup, the measurements from Falling Sphere are much more accurate. However, the Falling Sphere does not provide a continuous measurement of the ink viscosity. The readings are done in segments. Therefore, depending on your accuracy requirement Falling Sphere may or may not be suitable for your process.
Vibrational Viscometer measures the damping of an oscillating electromechanical resonator immersed in the sample fluid. This technique is often used in process to give continuous readings. Digital data are recorded continuously through sensors. Vibration Viscometer is the most accurate real time measurement instrument of the 3 mentioned.
To get an accurate and continuous reading of the ink viscosity is only the first step. The purpose of an accurate and continuous reading is so that you can adjust to it in real time. Many printing and converters are adopting the automatic ink viscosity control function to their operation. To automatically measure the ink viscosity in real time, and most important of all, to make adjustments in real time to maintain a stable viscosity throughout the printing operation.
The amount of labor, time and waste could be saved with the automatic ink viscosity control. Lets make a simple calculation
Scenario
- Lets say you have a one 6 color press
- On average you take on 30 jobs each week
- On average each of your job is 12,000 meters long
- Working hours per week is 40 hours. The printing operational time is 30 hours
- On average the ink viscosity should be measured and adjusted every 30 minutes
- On average it takes 3 minutes to measure the ink viscosity and 5 minute to adjust each color. A total of 8 minutes per color
- On average you spoil one bucket of good paint every week due to error during viscosity adjustment.
- Ink wasted from bad print
- Ink waste from a higher than needed viscosity
Waste Calculation
- Labor time wasted per year : 138,240minutes
- Ink wasted per year : 192 buckets
Financial Waste Calculation
- Labor: 138,240 minutes x ( USD 17 per 60min ) = USD 39,168
- Ink: 192 buckets x (USD 200 per bucket) = USD 38,400
- Reputation cost due to bad print = unmeasurable
Financially you can easily get USD 77,568 of savings per year from an automatic ink viscosity control system. In terms of the reputation cost due to bad print, the cost is unmeasurable.
At KYMC we offer the latest automatic ink viscosity control. Contact us now to learn how you can benefit from it.
Article by Daywey Chen, KYMC