Steps to help you reduce your production lead time
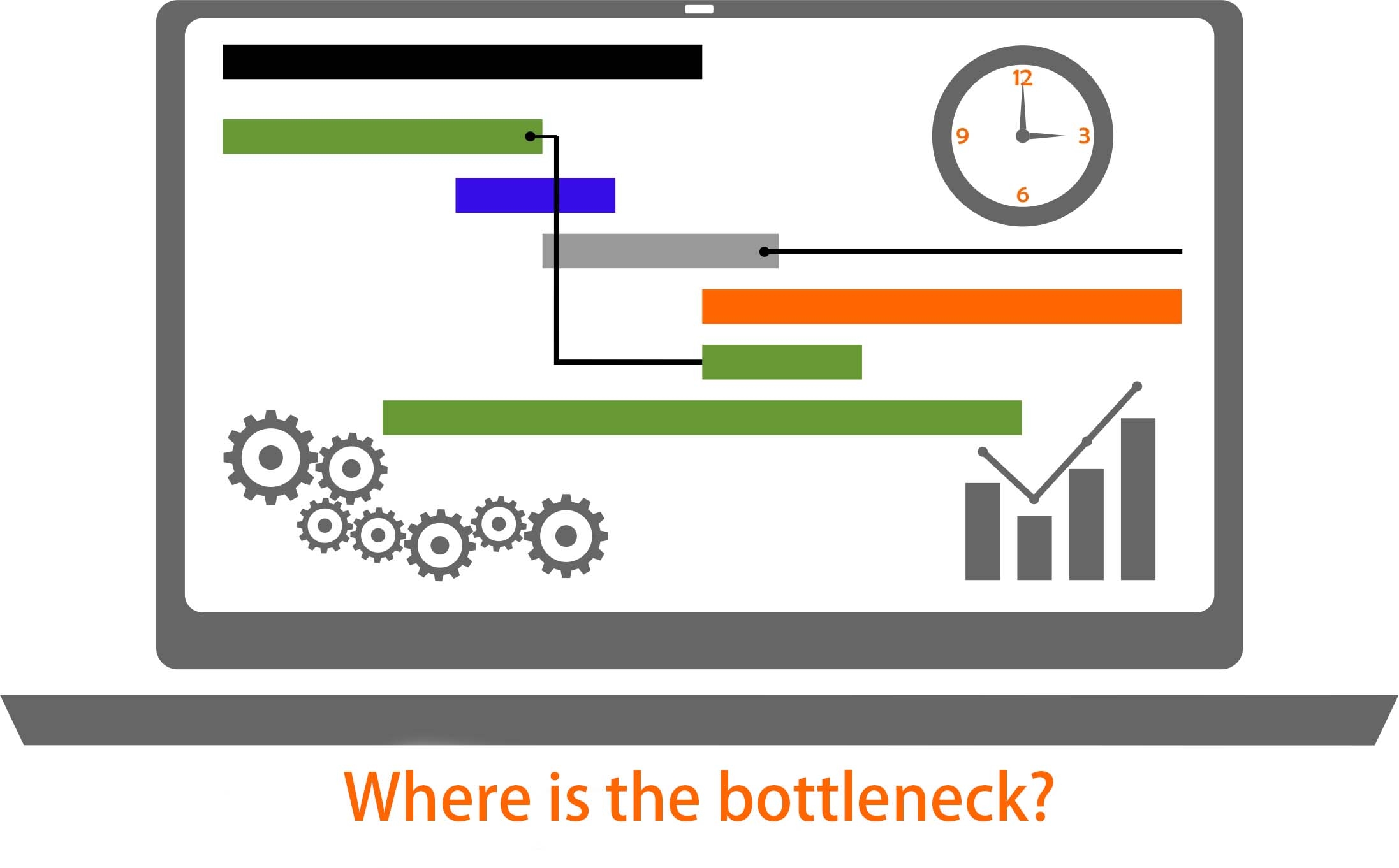
As the market demands for faster delivery time. It is the challenge of the printers & converters to shorten their lead time. There are many ways to improve the production lead time. First of all, you need to have a decent scheduling system in place to schedule your work efficiently. The same sets of production machinery and tools can produce different results depending on how effectively you schedule your work. To effectively schedule your production there are a few processes to guide you through
1. Identify which is the longest job in your factory. The longest job in your factory will become the shortest lead time for the system
2. Once you start scheduling try to minimize the amount of idle time for each machine in the system before it completes all the required job of the day.
3. When scheduling, try to get as close to your shortest lead time identified in step 1 as possible.
Once you have optimized your schedule you can identify where your bottlenecks are. Your bottleneck would be where your stocks are piling up as it has the lowest processing rate. The bottleneck is the area where the most accumulation is occurring. Accumulation occurs when your input comes in faster than the speed that you are able to process it at. For example, there are three processes A, B, and C in the system. In the system, the production process must go through process AàBàC in order. The area where inventories are piling up the most will be the bottleneck of your system.
When we want to decrease the overall lead time. It is important to look at your production process as a whole. As a system that consists of multiple machines working together in designed order. You shouldn’t look at each machine or station individually. Looking at each machine individually will likely to lead you to bark up the wrong tree with no overall lead time improvement at the end of the day.
Let's look at an illustrated example
There are 4 jobs that the factory needs to complete on Friday. The working hour of the factory is from 8:00 to 17:00, with a one-hour break for lunch.
Jobs
job 1 {5,000m job ; 35 min printing setup time ; 8 color)
job 2 {30,000m job; 20 min printing setup time ; 4 color)
job 3 {20,000m job; 20 min printing setup time ; 4 color)
job 4 {7,000m job; 25 min printing setup time ; 5 color)
Constraints
Production must be in the order of Printing à Coating à Slitting
Printing Press 1 {max production speed = 300m/min)
Printing Press 2 {max production speed = 150m/min)
Coating & Laminating {max production speed = 250m/min)
Slitter & Rewinder 1 {max production speed = 150m/min)
Slitter & Rewinder 2 {max production speed = 150m/min)
As demonstrated, different scheduling can produce different completion time of the 4 jobs. In schedule 1, the factory is not able to complete all 4 jobs before 17:00, furthermore, taking up much of the worker’s lunch break. Schedule 2 is clearly a more effective schedule, even though it takes up 30 minutes of the lunch break. The factory is able to complete all 4 jobs at 16:35
Lets try to shorten the lead time of the system (schedule 2) in two different ways
Method 1 - To upgrade printing press 2 from 150m/min to 300m/min
Method 2 - To upgrade the coating and laminator from 250m/min to 300m/min
As demonstrate with method 1, the upgrade of the printing press 2 shortened the production time of job 1 and job 4. However, having no impact on the total production time. In method 2, the upgrade of the coating and laminator decreased the total production time of the system to 16:25, and now only taking up 5 minutes of the worker’s lunch break.
The upgrade of printing press 2 has no effect on the overall production lead time because in this scenario printing press 2 is not the bottleneck. The bottleneck in the system is the coating and laminator. Off course since Slitting is the last process in the system. We can also improve the overall lead time of the system by speeding up the Slitting station.
In conclusion, it is important for plant managers to look that the system as a whole, to identify and target the bottlenecks in the system, and not to look at each station individually.