5S implementation in the printing & packaging industry
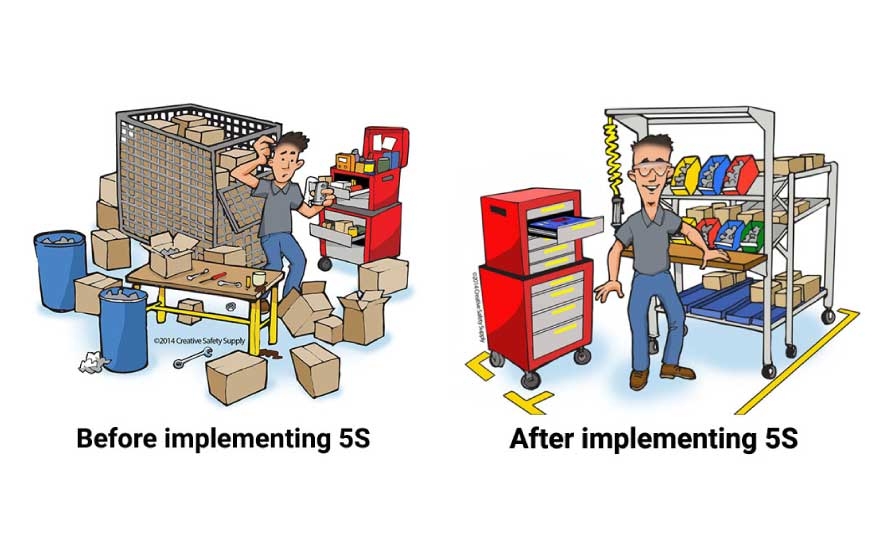
Most people have heard of 5S before, which stands for sort, set in order, shine, standardize, and sustain. 5S is a framework for visual management or visual control. 5S is about making the most efficient out of the workplace, where materials, tools, and equipment are organized in a logical location based on who needs them and how frequently are they needed. Successful implementation of the 5S program has proven to make the workplace function better by making it an easier place to work.
Sort: Sort through your materials, tools, and equipment. Remove everything that is not used to complete a work process from the work area.
Set in order: For the remaining materials, tools, and equipment in the work area, organize each item into its designated place. Organized them in a logical way that makes tasks easier for workers to complete. This includes placing items in ergonomic locations where the minimum amount of effort is needed to access them.
Shine: To proactively keeping the workspace clean. This involves routine task such as mopping, dusting, performing maintenance on machinery, tools and other equipment.
Standardize: To take the first 3S’s and make rules out of it to become the organizational standard for employees and management to follow.
Sustain: To sustain the 4S’s over time. To continue the practice and to conducts audits to maintain discipline. At the same time to make continuous improvement.
How to implement the 5S into the printing and packaging industry? Adopting the 5S program is not the job of the managers, but it is important for all the employees to embrace the visual management culture. Employees should all understand how the program can be effective and are able to work towards higher levels of efficiency. All the employees should be involved in nearly all stages of the 5S implantation. This includes participating in the decision-making process regarding what should remain in the working area and what should be abandoned. For the materials, tools, and equipment that remains in the working area, what are the importance levels? What is the usage frequency? From here, decide on a logical placement in the workspace.
Part of adopting the 5S program, is to utilize supporting tools to help with the process. To make the process more efficient and easier. These tools can include sleeve rack for better storage of the printing and anilox sleeves, shelves for the better storage of paint buckets, shadow boards to align each working tools so that a missing piece can be spotted easily, floor markings so that materials can be placed in an organized manner and at the same time defining the boundaries of each workstation for a more efficient production route, signs and labels to alert the employees of dangers and to describe the items.
The 5S program in a way is the prerequisite to adopting lean manufacturing. Through the 5S program, the workspace becomes cleaner and more organized so that the enterprise is ready for the next step of continuous improvement.
Relevant Reading
OEE (Overall Equipment Effectiveness) for Printing
5S implementation in the printing & packaging industry
Better machine communication through OPC-UA
Article by Daywey Chen, KYMC