Establish Your Barrier Coating Solution Now
June 16, 2024 | KYMC Marketing
2024-06-16
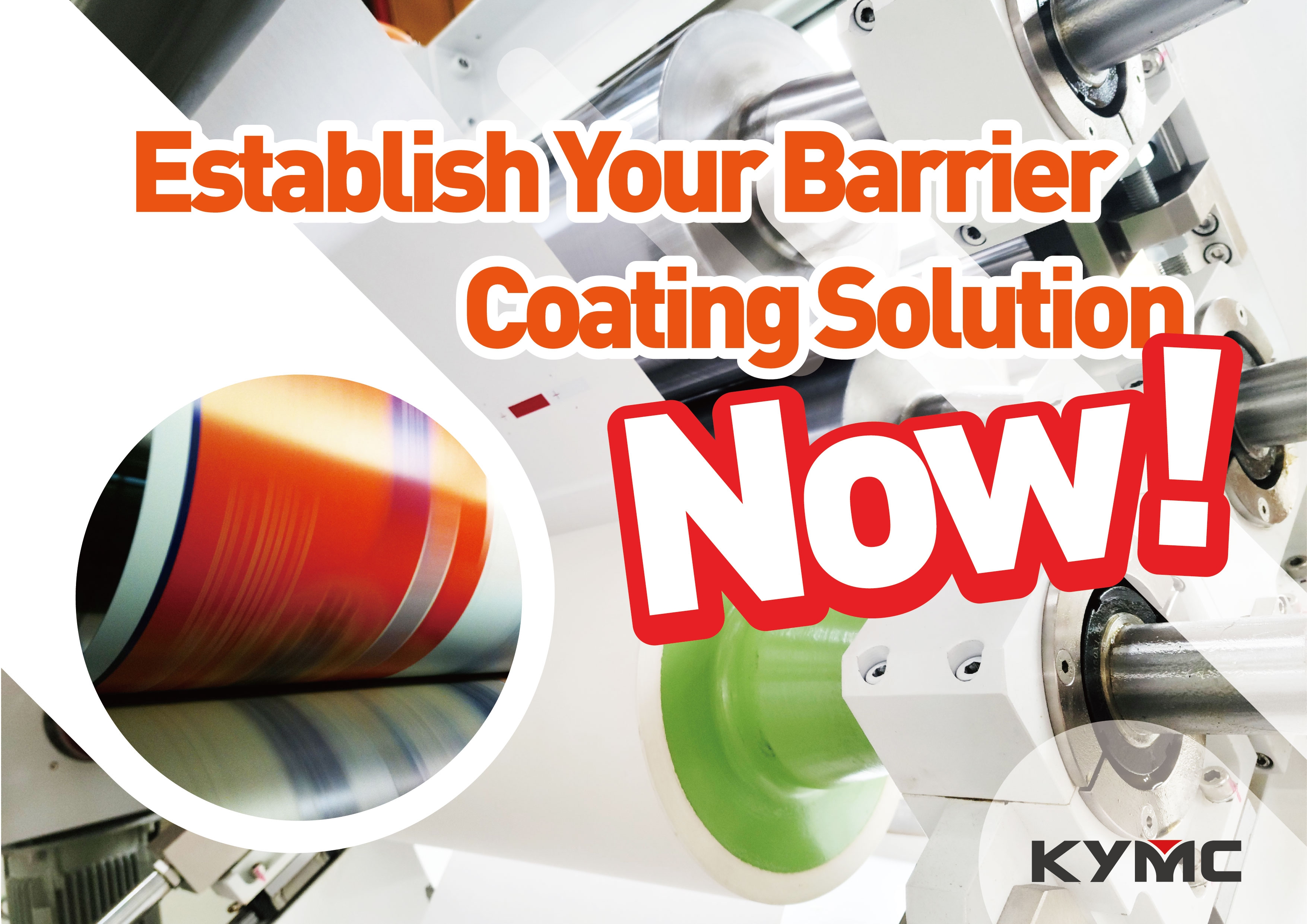
Over the drupa 2024 period, we have received ample requests regarding barrier coating. Therefore, we have decided to summarize the barrier coating solutions that we offer in case you missed us during drupa. It did not come to our surprise that many industry leaders were interested in finding or upgrading their barrier coating solutions as coating demand is on the rise due to an increase in environmental consciousness. The trend of replacing multi-layer materials with mono material will require a coating to provide the barrier functions needed. According to Smithers, the global coating market is expected to increase to $10.79 billion in 2028. The volume demand will accelerate, and to make sure that you don’t miss out on this opportunity, finding the right solution partner with suitable equipment technologies is critical.
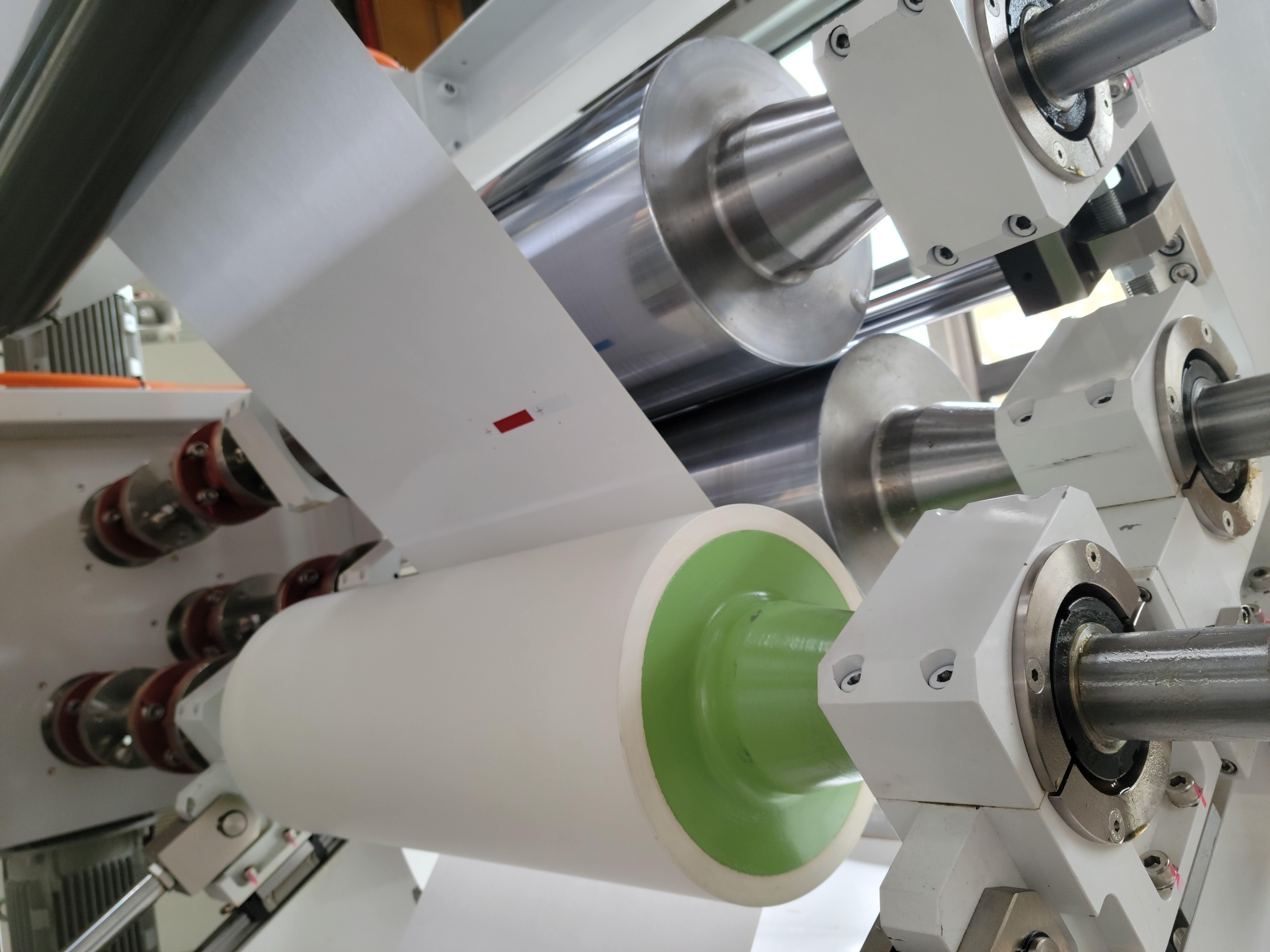
Without further ado, let’s jump into the KYMC barrier solutions. During drupa 2024, we have been asked to provide a flexible barrier coating solution by many of our visitors. When it comes to flexibility, KYMC offers coating equipment in two different forms. As a standalone (offline) barrier solution, or as a coating unit that is integrated into the printing operation. Each form has its pros and cons. If coating is conducted on a highly dynamic process. For instance, coating is to be combined with different printing operations, such as gravure printing, flexo printing, digital printing…etc. or combined with different processes such as film extrusion, sheeting, die cutting…etc. In this case, standalone (offline) barrier equipment may be more suitable. A standalone (offline) will allow you to decouple your coating with whatever upstream or downstream process is needed for the job. If coating is to be conducted on a relatively fixed operation repeatedly for long-run jobs. For instance, going through printing first, then coating repeatedly. In this case, integrated hybrid equipment to combine the two processes together will significantly improve production efficiency. The integrated hybrid equipment can reduce the amount of setup time needed and eliminate the waste created during process changeover.
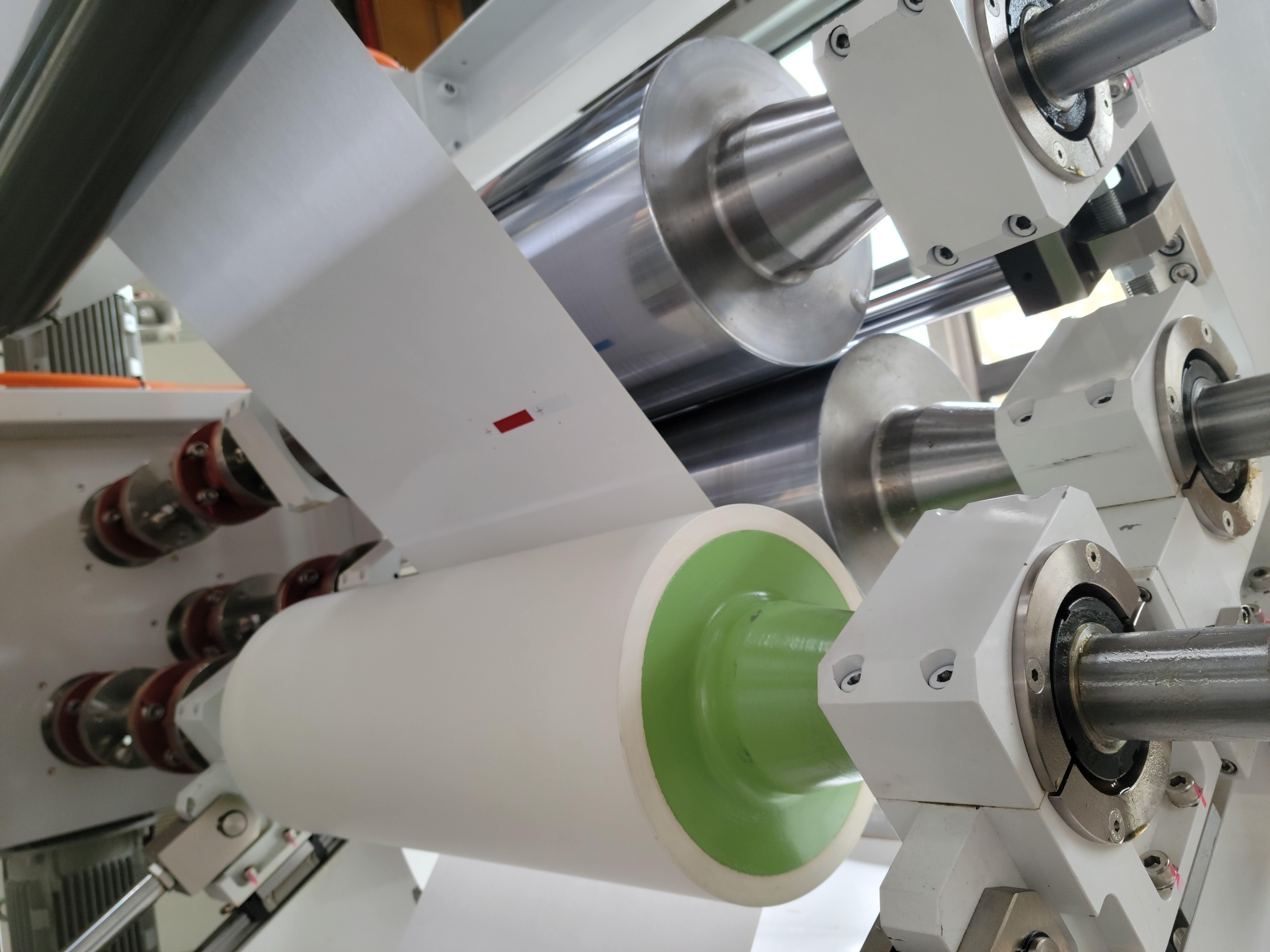
Without further ado, let’s jump into the KYMC barrier solutions. During drupa 2024, we have been asked to provide a flexible barrier coating solution by many of our visitors. When it comes to flexibility, KYMC offers coating equipment in two different forms. As a standalone (offline) barrier solution, or as a coating unit that is integrated into the printing operation. Each form has its pros and cons. If coating is conducted on a highly dynamic process. For instance, coating is to be combined with different printing operations, such as gravure printing, flexo printing, digital printing…etc. or combined with different processes such as film extrusion, sheeting, die cutting…etc. In this case, standalone (offline) barrier equipment may be more suitable. A standalone (offline) will allow you to decouple your coating with whatever upstream or downstream process is needed for the job. If coating is to be conducted on a relatively fixed operation repeatedly for long-run jobs. For instance, going through printing first, then coating repeatedly. In this case, integrated hybrid equipment to combine the two processes together will significantly improve production efficiency. The integrated hybrid equipment can reduce the amount of setup time needed and eliminate the waste created during process changeover.
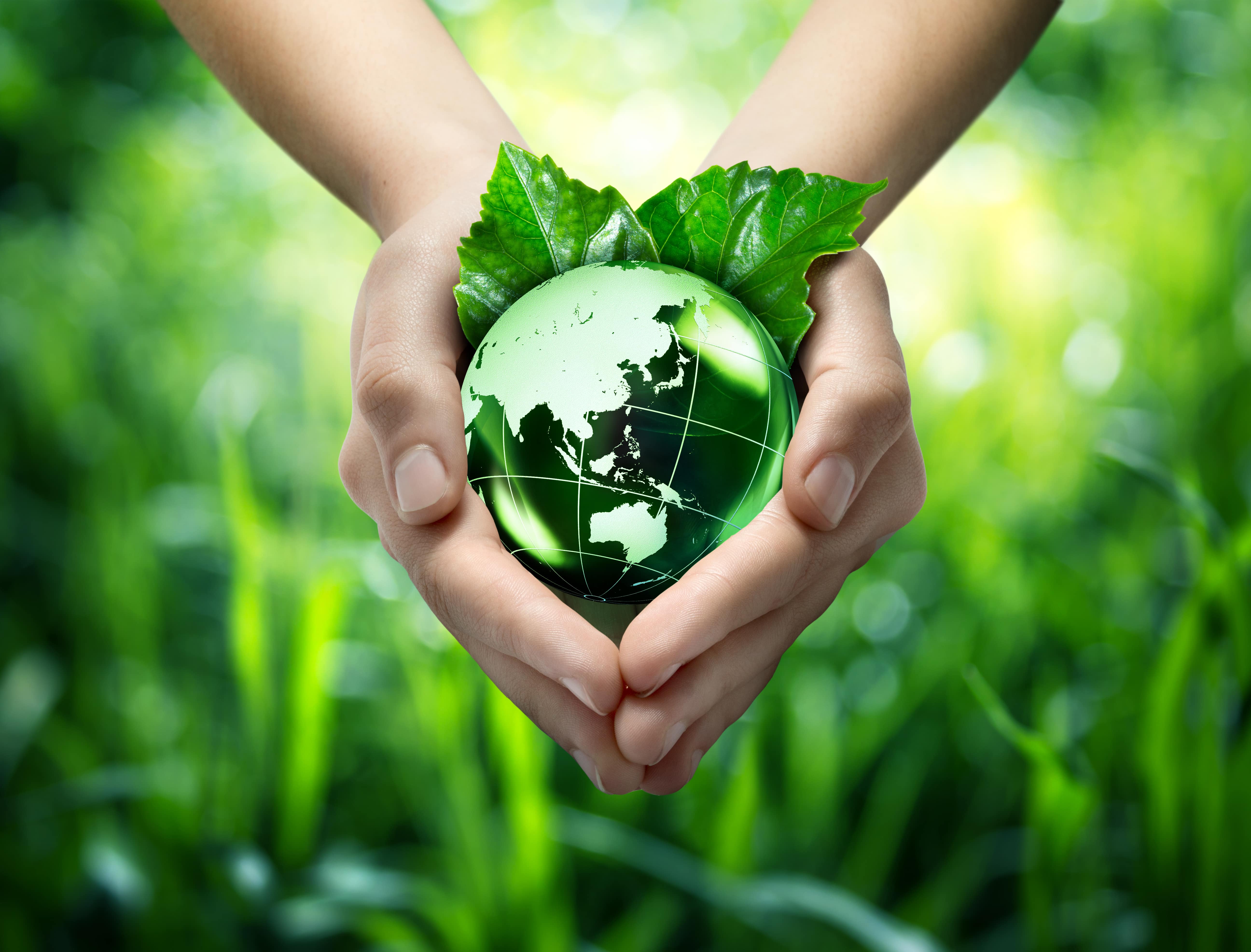
Furthermore, drying capability is the most important aspect we consider when designing a water-based coating production line. As 99% of the new-generation barrier coating materials are aqueous, the drying performance of the coating equipment almost entirely determines the production speed of the whole coating line. Designing a reasonable barrier coating production speed and its drying system relies heavily on experience with water-based barrier materials. At KYMC, we design drying systems based on the coated weight requirement and the characteristics of common water-based barrier materials in the market, or we can design the drying capacity of the coating equipment through meticulous calculations based on the specific barrier material you specify. Our principle in providing equipment is to prioritize realistic production efficiency and space utilization to ensure you achieve the best return on investment. To achieve this goal, we offer various drying methods suitable for your facility, including conventional hot air dryers, IR ovens, NIR rapid moisture removal equipment, and hybrid drying systems.
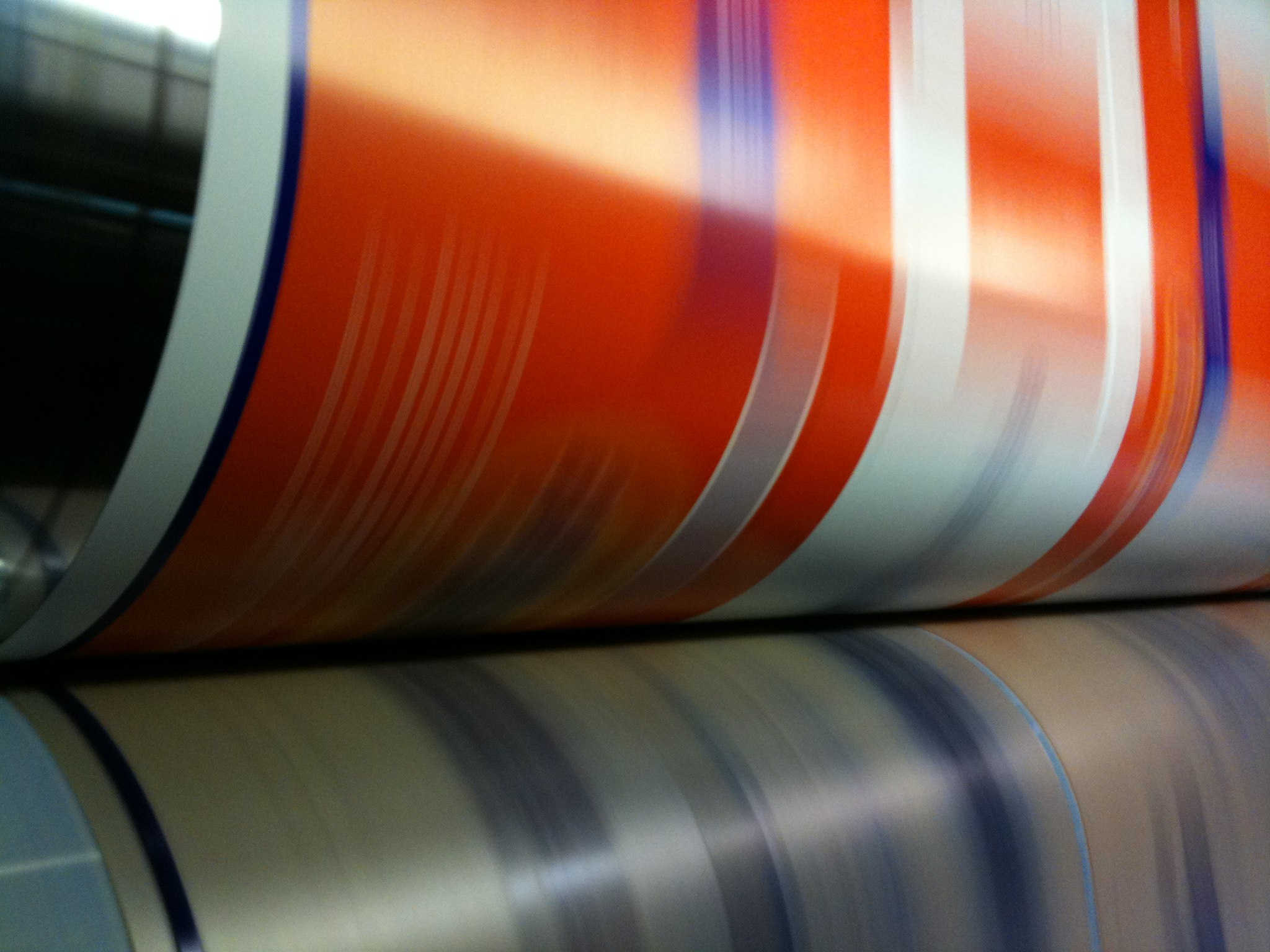
drupa 2024 was a great success for KYMC. We were happy to interact with many of our existing customers and at the same time get acquainted with many new friends. We work with our customers to deliver a customized solution that matches the customers’ needs. We believe that optimal solutions are established based on back-and-forth input and feedback, testing when necessary, and the experience of both parties. If you are looking to establish your own barrier solution or looking to upgrade your existing barrier solution, reach out to our representatives, and we are more than happy to start a discussion with you.
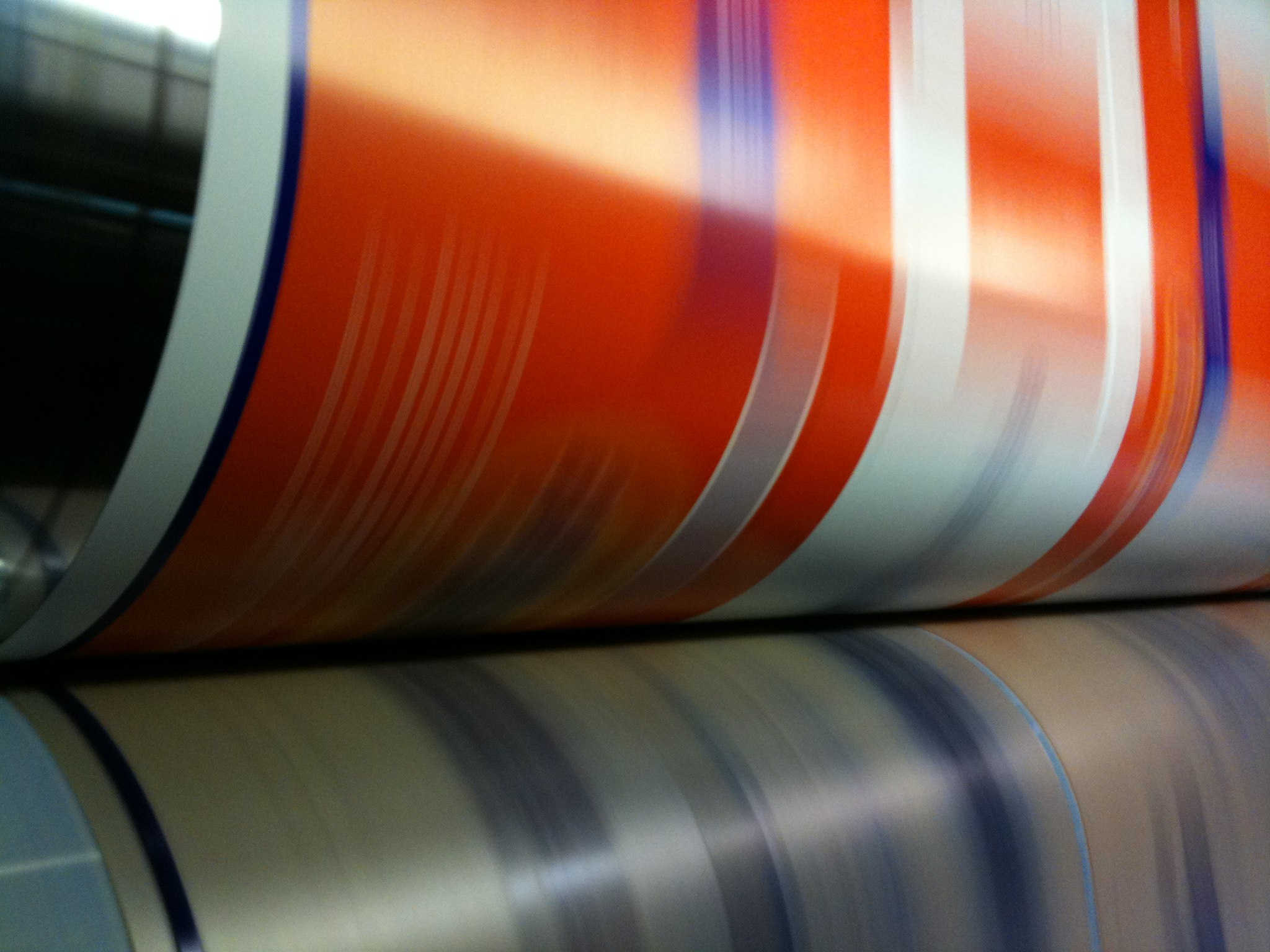
drupa 2024 was a great success for KYMC. We were happy to interact with many of our existing customers and at the same time get acquainted with many new friends. We work with our customers to deliver a customized solution that matches the customers’ needs. We believe that optimal solutions are established based on back-and-forth input and feedback, testing when necessary, and the experience of both parties. If you are looking to establish your own barrier solution or looking to upgrade your existing barrier solution, reach out to our representatives, and we are more than happy to start a discussion with you.